
What is cable tray machine process?
2025-04-29 12:00Cable tray machine is an indispensable equipment in modern electrical engineering and is widely used in the production of cable trays. As an important structure to support insulated cables for power distribution, control and communication, cable trays have become a standard solution for cable management in various industrial and commercial buildings. In this article, KINGREAL will discuss in detail the process flow, machine advantages and importance of cable tray machine in practical applications.
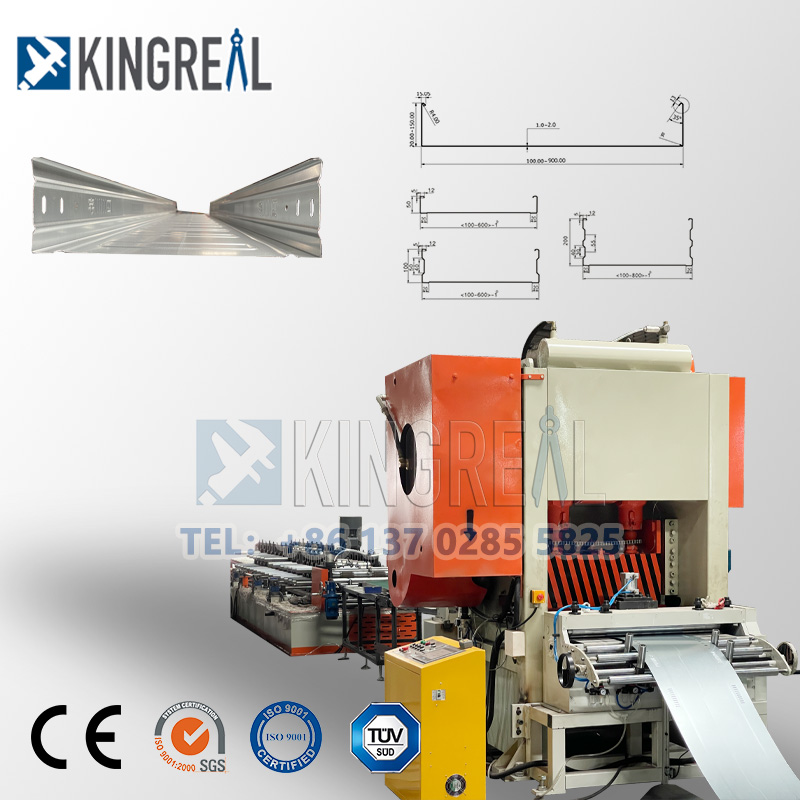
Components of Cable Tray Machine
Cable tray roll forming machine consists of multiple precision parts, each of which plays a vital role in the entire production process. The main components of cable tray machine include:
Decoiler: responsible for unwinding the coil to provide a basis for subsequent processing. The design of the decoiler ensures the flatness of the material during the unwinding process and avoids processing problems caused by material warping.
Preciison leveling machine: The unwinding material is leveled to eliminate any deformation of the material and make it suitable for subsequent processes. The precision leveling machine ensures a smooth and flat surface of the material by adjusting the pressure and speed.
Hydraulic punching station: At this stage, the material is punched according to the design requirements. The punching process is an important part of the cable tray forming process to ensure the functionality and aesthetics of the product.
400-ton hydraulic punching press: This equipment is used to punch the material with high precision. The punching press works in conjunction with the punching station to punch holes in different locations of the material to meet design requirements.
Main roll forming machine: This is the core equipment for cable tray forming. The leveled and punched material is fed into the roll forming machine, and the forming roller is used to press the material into shape to produce cable trays of various specifications.
Cut-to-length machine: The formed cable tray will be sheared through the cut-to-length machine to ensure that the length of the product meets the customer's requirements. This step also requires high-precision equipment to ensure product consistency.
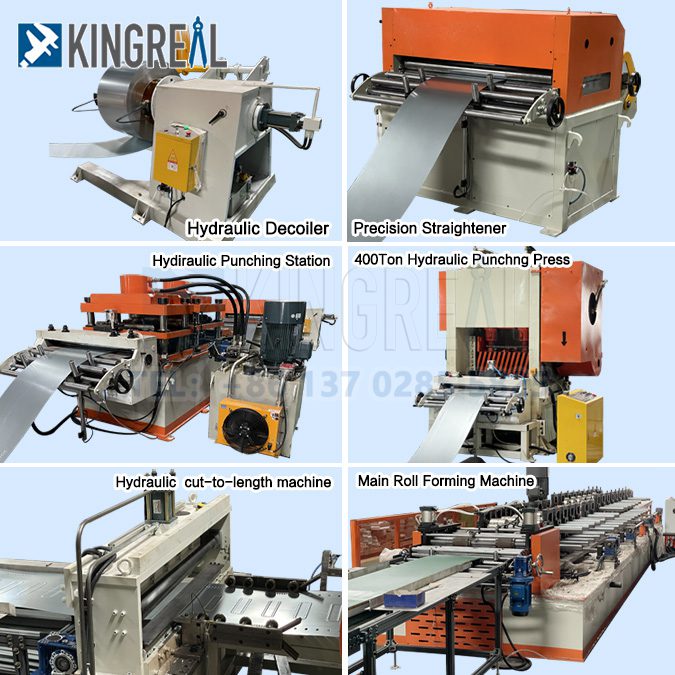
Functions and Applications of Cable Trays
Cable tray machine can produce different types of cable trays, the main function of the cable tray system is to support cables, and its application fields are wide, mainly including:
Replacing traditional cable management systems: Cable trays can effectively replace traditional open wire or wire tube systems, providing safer and more flexible wiring solutions for cables.
Adapt to various environments: Cable trays can perform well both indoors and outdoors, can withstand different environmental conditions, and provide a safe passage for cables.
Overhead or underground laying: Cable trays are particularly suitable for overhead or underground laying of large amounts of data cables, and are widely used in industrial, commercial and communications fields.
In addition, cable trays are often called wire baskets, wire troughs or ladder racks. Due to their superior performance and flexible application, they have become an important part of modern electrical engineering. This is why the demand for cable tray machines is high. |
Workflow of Cable Tray Roll Forming Machine
The workflow of the cable tray machine can be divided into the following main steps:
1. Unwinding
The decoiler unwinds the coil to ensure that the material is flat. This step is the first step in the entire production process and directly affects the subsequent processing quality. During the unwinding process, the equipment can automatically adjust the unwinding tension to ensure the smooth unwinding of the material.
2. Leveling
The precision leveling machine levels the unrolled material to eliminate warping and deformation. During this process, the pressure and speed of the precision leveling machine will be adjusted according to the characteristics of the material to ensure the best effect.
3. Punching
After the material enters the punching station, it is punched according to the design drawings. The accuracy and position of the punching are key factors affecting the quality of subsequent forming. At this time, the punching station and the 400-ton hydraulic punching press work together to ensure high-precision punching in different areas.
4. Forming
The roll forming machine is the core part of cable tray machine. The flattened, punched and pressed material is fed into the roll forming machine, and the equipment presses the material into shape through the forming roller to generate different types of cable trays. These trays can be Solid bottom cable tray, Trough cable tray, Channel cable tray, Perforated cable tray, Non-perforated cable tray and Trunking cable tray.
5. Cutting
The formed cable tray is cut according to the customer's preset length through the cut-to-length machine to ensure that the length of each product meets the customer's requirements. This step requires high-precision shearing equipment to ensure the neatness and consistency of the product.
Advantages of Cable Tray Roll Forming Machine
The cable tray machine has the following advantages, making it popular in the market:
1. Fully automatic width adjustment The cable tray roll forming machine can automatically adjust the production width within a few seconds, and the product width can be adjusted between 200-600mm. Through the computer control system, users can set it according to production needs, greatly improving production efficiency. | ![]() |
![]() | 2. Monitoring function and fault detection function The cable tray machine is equipped with real-time monitoring function, which can timely feedback the production status and ensure the smooth progress of the production process. In addition, the built-in fault detection system can quickly identify cable tray roll forming machine failures, reduce downtime and improve production efficiency. |
3. Diversified product types The cable tray roll forming machine can produce various types of cable trays to meet the needs of different customers, thereby enhancing the market competitiveness of enterprises. | ![]() |
![]() | 4. Diversified processing materials The cable tray machine can process a variety of materials, including hot-dip galvanized steel, pre-galvanized steel, hot-rolled and cold-rolled steel, stainless steel and aluminum, etc., to adapt to different working conditions and customer needs. |