
Sheet Metal Perforation Line
KINGREAL is committed to providing customers with the best quality Sheet Metal Perforation Line manufacturing solutions with advanced technology and rich experience. To meet the increasing market demand for high-quality, precision perforated products.
- KINGREAL
- China
- 80 Days
- 9999
- Information
- Download
Video About Coil Perforation Line
Definition of Sheet Metal Perforation Line
KINGREAL provides perforated metal machines according to customer needs to meet specific needs. KINGREAL provides coil perforation lines suitable for different perforation shapes, thicknesses, raw materials, etc., and are committed to providing customers with the ultimate perforated sheet solutions. By using KINGREAL perforated metal machines, customers can further process and manufacture various products such as perforated wall panels, perforated filter elements, perforated screens, perforated silencers, perforated panel trays, perforated ceilings, etc. to meet the needs of different fields.
In order to better meet market needs, KINGREAL Coil Perforation Lines are divided into three main types: the punching lines are metal ceiling perforation lines, coil to coil perforation lines, and sheet metal perforation line.
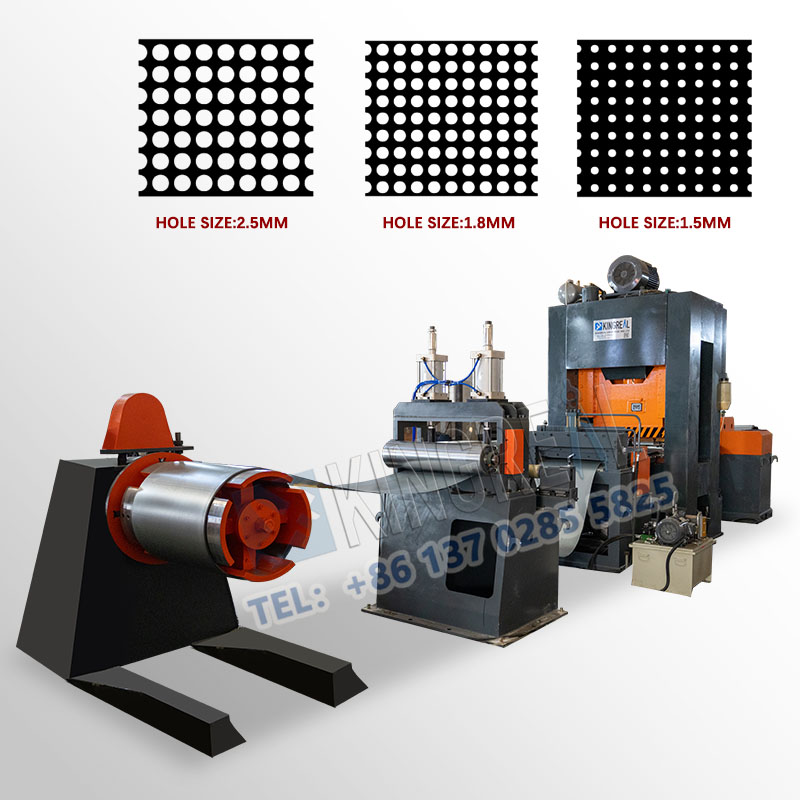
Advantages of KINGREAL Coil Perforation Lines
(1) Easy to operate
KINGREAL coil perforation lines are designed to be user-friendly, equipped with an intuitive control panel and advanced software system. This design enables operators to easily master the workflow when using the perforated metal machine, greatly reducing training time and operating difficulty. Even beginners can become familiar with and fully control the various functions of the coil perforation line in a short time after simple training.
(2) Flexible configuration
KINGREAL perforated metal machine shows great flexibility in configuration, which can meet the personalized needs of different customers. KINGREAL provide a variety of speed levels and punching tool designs, and customers can choose faster or slower punching strokes according to actual production needs. This flexibility not only improves production efficiency, but also enables the coil perforation line to adapt to the processing needs of various materials, such as metal sheets of different thicknesses and hardness. Customers can choose the most suitable configuration according to their budget and production plan to obtain the best cost-effectiveness.
(3) Efficient production capacity
KINGREAL perforated metal machine adopts advanced manufacturing technology, combined with efficient production processes, to ensure that each link is as efficient as possible, thereby reducing the overall operating cost. KINGREAL coil perforation line can complete a large number of punching tasks in a short time, greatly improving the production efficiency of customers.
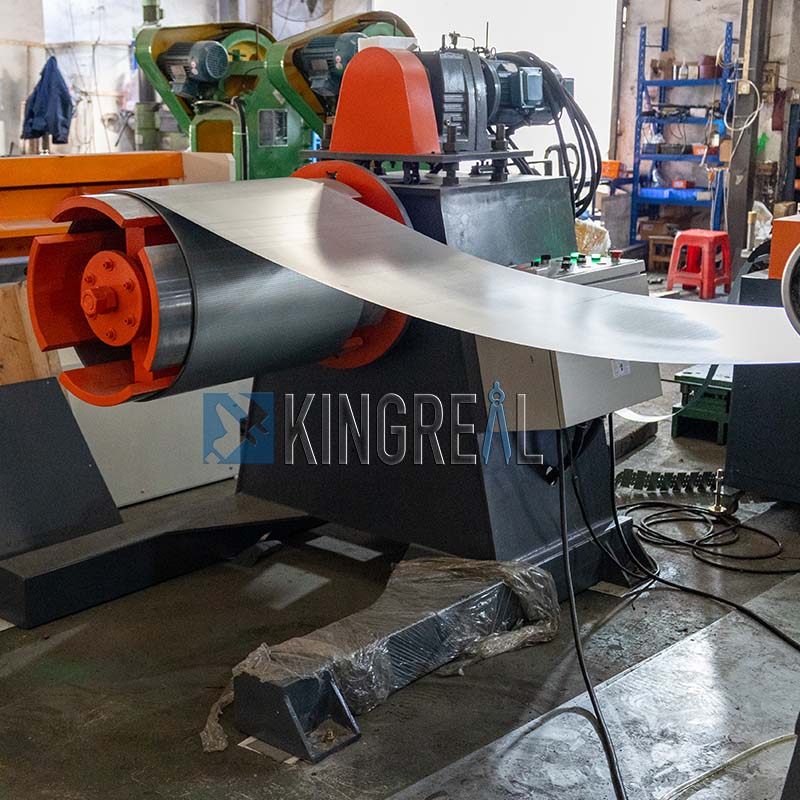
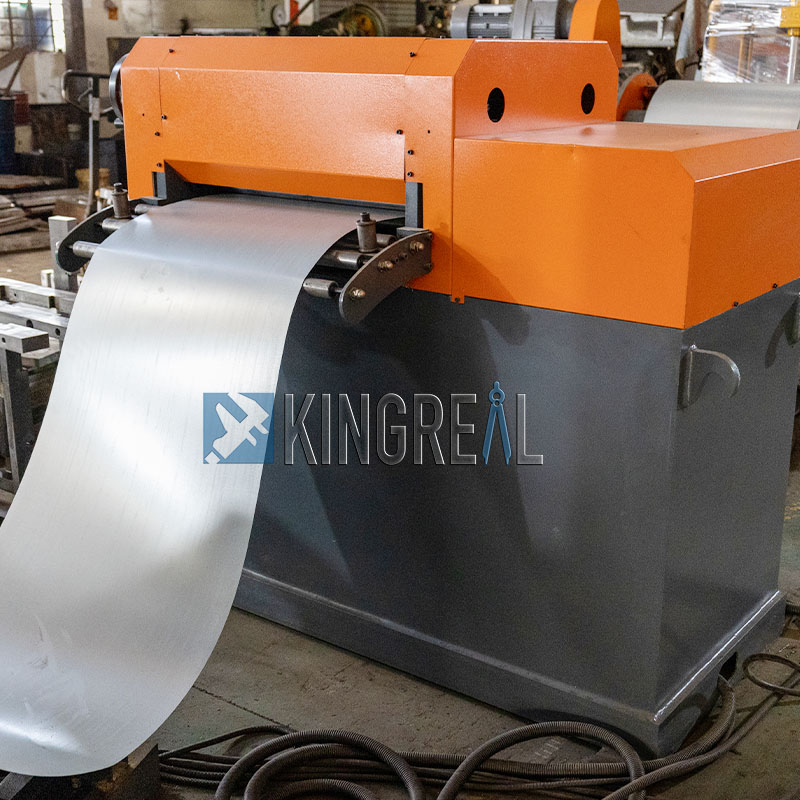
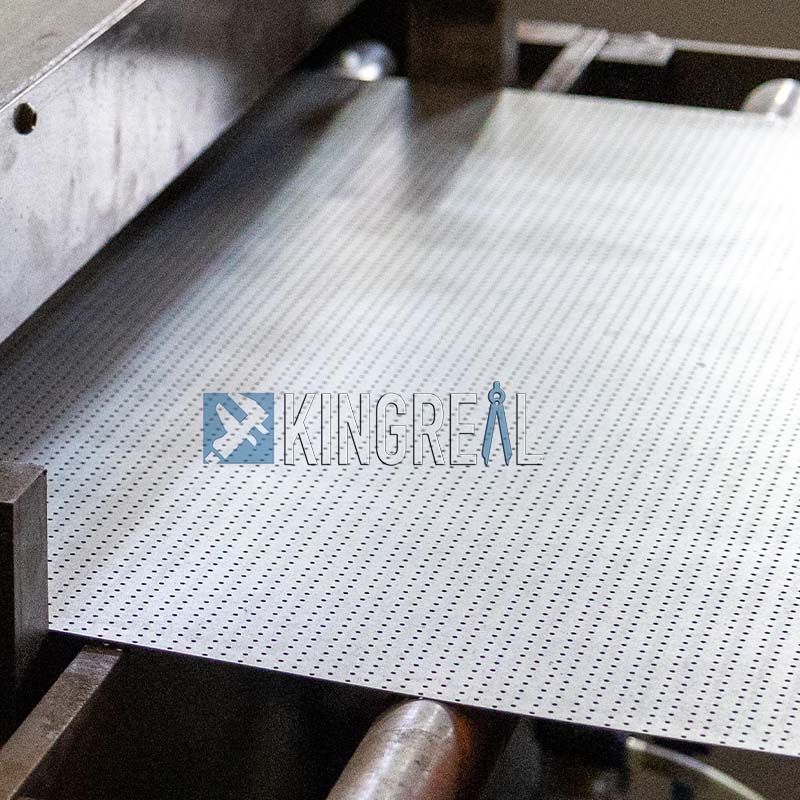
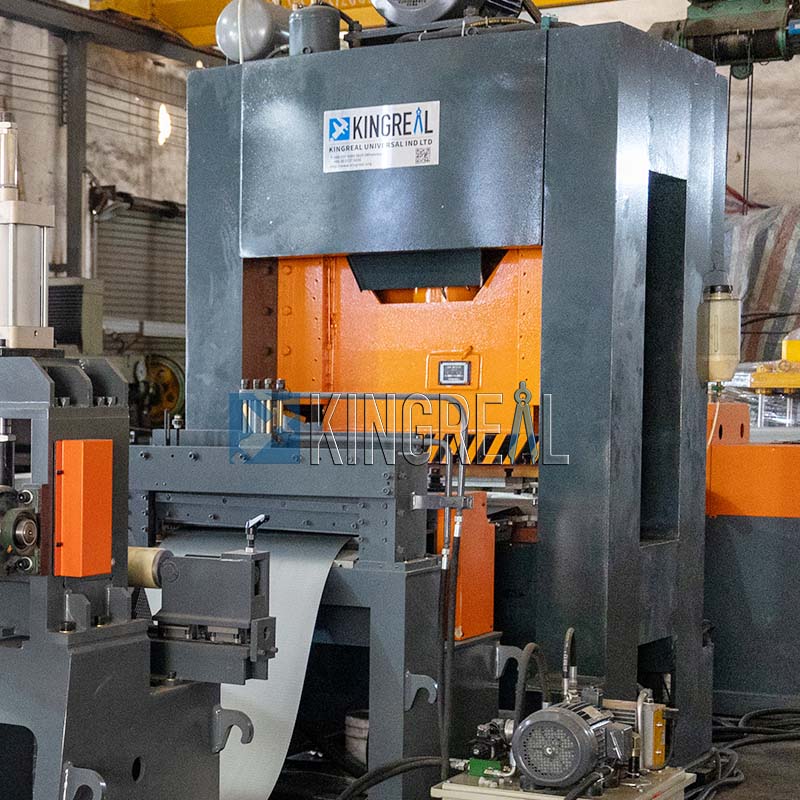
Coil Perforation Lines with Different Configurations
In addition to the metal ceiling perforation line, KINGREAL has also designed a coil to coil perforation line and a sheet metal perforation line according to different punching processes.
![]() | |
Coil to coil perforation line: The main function of KINGREAL coil to coil perforation line is to wind up the metal coils that have been punched, ensuring that the metal surface is not scratched during transportation and storage, and at the same time facilitating subsequent secondary processing. | The perforated metal machine with cutting is another important equipment of KINGREAL, focusing on the precise cutting of perforated metal coils to meet customers' requirements for finished product length. |
Working principle: The workflow of the coil to coil perforation line is relatively simple but efficient. First, the decoiler unwinds the metal coil and corrects it through the leveler to ensure the flatness of the material. Subsequently, the punching machine punches according to the preset parameters and punches the required hole shape and aperture on the material. Finally, the perforated metal material is wound up by the recoiler to form a roll that can be transported and stored. | Working principle: The workflow of the sheet metal perforation line is also simple and efficient. First, the decoiler unwinds the metal coil and corrects it through the leveler. Then, the punching machine punches according to the preset parameters. Finally, the perforated material enters the cutting station and is precisely cut according to the length set by the customer to form the final product. |
Main components: -Decoiler -Precision straightener -Punching press -Recoiler
*Recoiler: The recoiler rewinds the perforated metal coil to form a neat roll. The equipment is exquisitely designed to effectively avoid scratches or damage to the metal surface during the winding process, and it is also convenient for subsequent transportation. Through the automated workflow, KINGREAL coil to coil perforation line significantly improves production efficiency, reduces the need for manual intervention, and reduces human errors. | Main components: Decoiler Precision straightener Punching press Cutting station
*Cutting station: The cutting station is the core part of the Sheet Metal Perforation Line, which can accurately cut the perforated metal coil according to the length preset by the customer. This process ensures that the size of each finished product meets the requirements, which is convenient for subsequent processing and use. |
Different Applications of Coil Perforation Lines
KINGREAL sheet metal perforation lines have a wide range of applications and can meet the needs of various industries. Here are some common industries and their specific finished products:
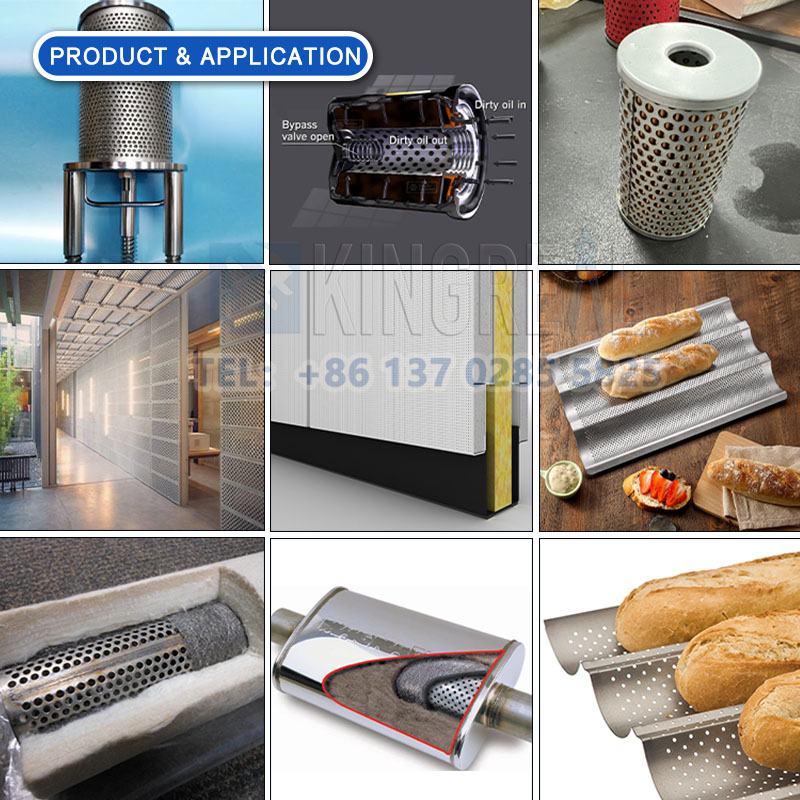
Construction industry: perforated wall panels, partition materials
Automotive manufacturing: perforated filter elements, silencers
Electronic products: perforated panels, radiators
Home appliance industry: perforated trays, ventilation nets
Environmental protection industry: perforated screens, wastewater treatment equipment
Whether it is a large enterprise or a small studio, KINGREAL sheet metal perforation lines can provide efficient and reliable solutions to help customers improve their production capacity.
KINGREAL Sheet Metal Perforation Line Innovation - Micro Punching Technology
In order to remain competitive in the industry, KINGREAL continues to work on technological innovation. KINGREAL has made significant progress in micro punching technology and successfully provided customized solutions for customers in Greece and Morocco.
![]() | ![]() |
-Greek case- For Greek customers, KINGREAL sheet metal perforation line is able to punch out micro holes with a diameter of only 1.0mm. This technological breakthrough not only meets customers' demand for high precision, but also demonstrates KINGREAL strong strength in the field of micro-punching. | -Moroccan case- For Moroccan customers, KINGREAL sheet metal perforation line can achieve micro-holes with a diameter of 1.5mm. This technology also faces great challenges, because micro-holes have extremely high requirements for the manufacturing of punching dies. |
*Technical Difficulty Analysis
The manufacturing difficulty of micro-holes is mainly reflected in the design and processing of punching dies. The common hole diameters on the market are 1.8mm and 2.5mm, and KINGREAL has successfully developed holes with smaller diameters, thanks to the continuous efforts and innovative thinking of KINGREAL engineers. During the research and development process, KINGREAL engineers first conducted an in-depth analysis of the existing punching dies to understand their shortcomings in the production of micro-holes. Subsequently, through the optimization of material selection, mold design and processing technology, the successful manufacture of micro-punching dies was finally achieved.
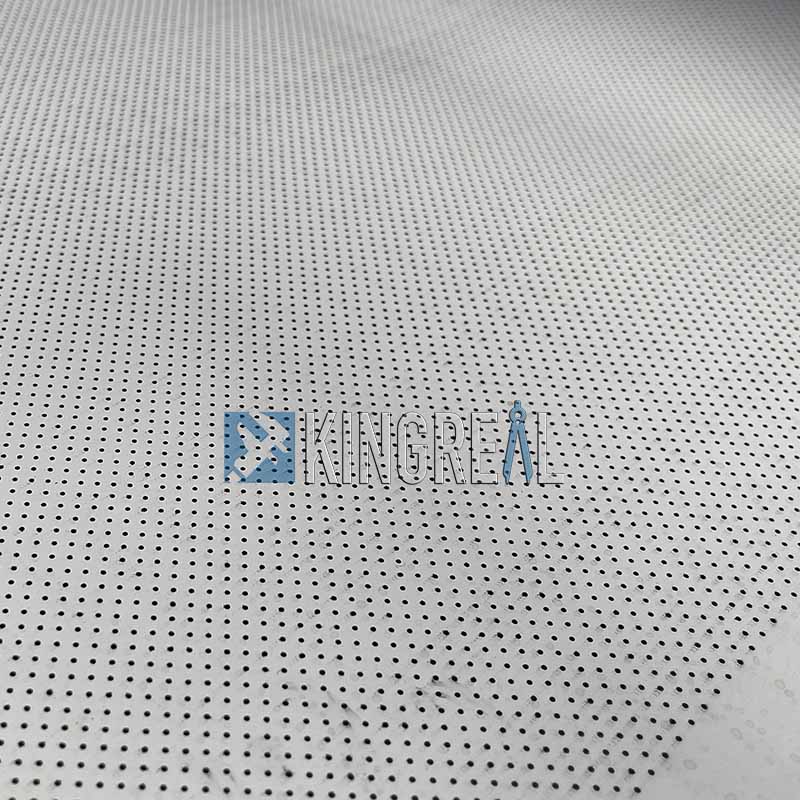
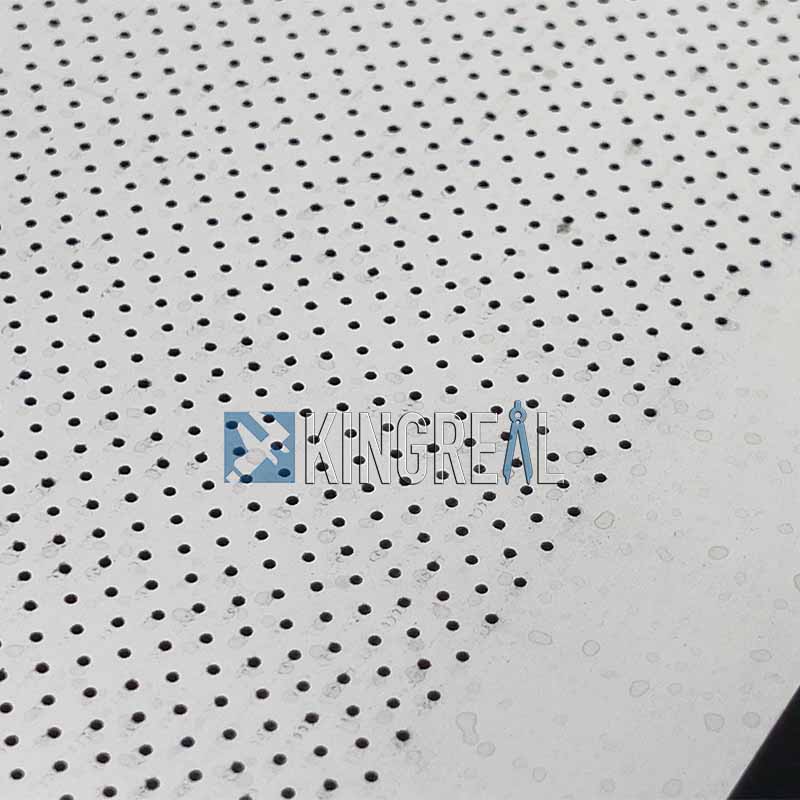
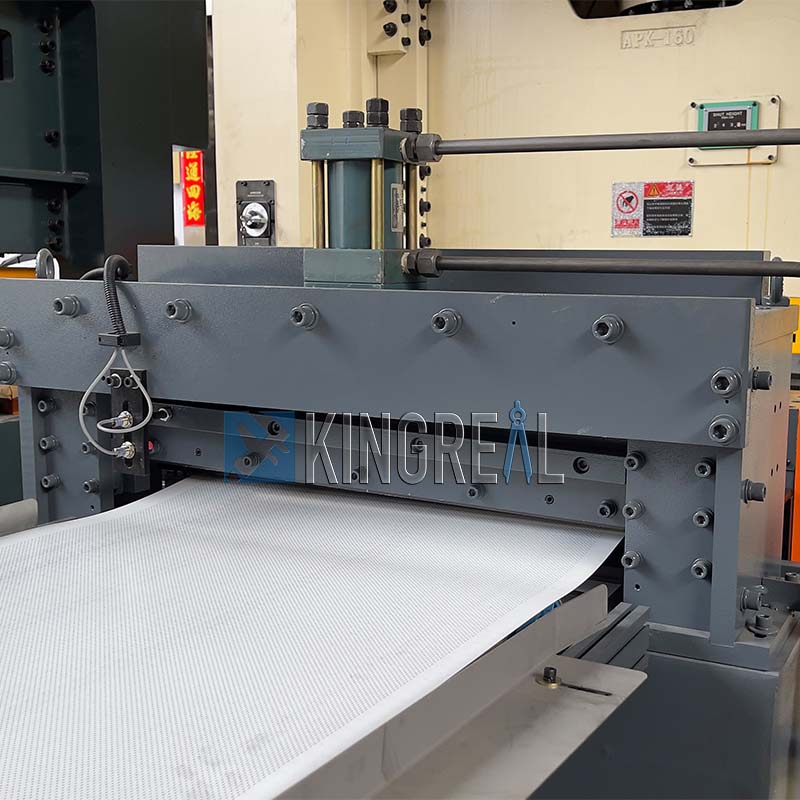
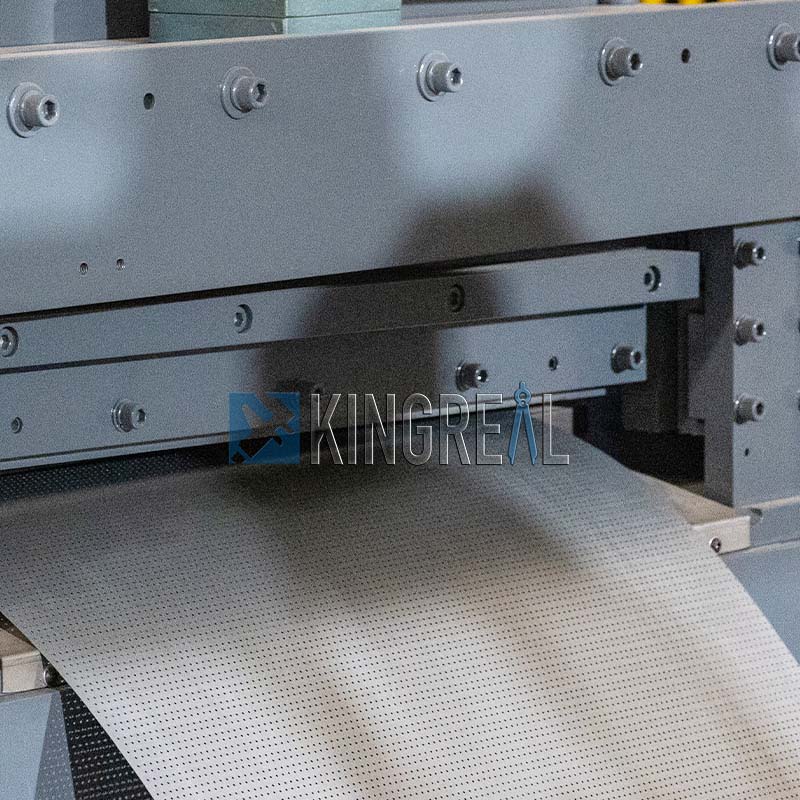
*Design and manufacturing process of micro-punching dies:
1. Punching die design
The design requirements for micro-holes are very strict, especially in terms of hole diameter and hole spacing. KINGREAL engineers need:
Accurate calculation: The size of micro holes is very precise, usually 1.0mm and below, and any slight deviation may result in unqualified products.
Complex geometry: In addition to standard circular holes, micro punching dies also need to be able to support holes of various shapes, which places high demands on the design complexity of the die.
Mold strength: Micro hole dies are subjected to great pressure during the stamping process, so the strength and wear resistance of the mold material must be ensured to prevent deformation or damage during the production process.
2. Material selection
The choice of materials directly affects the performance and service life of the mold. For micro punching dies, the material selection needs to consider:
High hardness materials: To ensure that the mold does not deform under high temperature and high pressure, high alloy steel or other high hardness materials are usually required.
Corrosion resistance: During the punching process, the generation of lubricating oil and metal chips may cause mold corrosion, so the material needs to have good corrosion resistance.
Processability: Micro hole dies are difficult to process, and the machinability of the material directly affects the manufacturing efficiency and precision of the mold.
3. Processing Technology
The processing technology of micro-holes is the key to achieve high-precision punching, and it mainly faces the following challenges:
Precision processing technology: High-precision processing equipment, such as CNC machine tools, laser cutting, etc., is required to ensure that the size and shape of the mold meet the design requirements.
Complex processing steps: The manufacture of micro-hole molds usually involves multiple processes, including cutting, grinding, heat treatment, etc., and any error in any process may lead to defects in the final product.
High technical requirements: Operators need to have rich experience and expertise to effectively control the processing and ensure the accuracy and performance of the mold.
4. Quality control
In the manufacturing process of micro-hole molds, quality control is crucial, mainly reflected in:
Strict testing standards: Each mold needs to be strictly tested for size and shape to ensure that it meets the design specifications.
Feedback mechanism: Timely data collection and analysis during the production process to make real-time adjustments to the mold to ensure the stability and consistency of production.