
What is the cut to length machine process?
2024-09-23 17:22The metal cut to length machine is also known as steel coil cut to length line, ctl line, coil cut to length line. It is simple and reliable to operate, and the stacking is neat. It has a high degree of automation, high precision in fixed length, and high flatness of the sheet. The metal cut to length machine is mainly composed of a frame, a knife holder, a drive motor, a transmission mechanism, a cutting device, etc. According to the required shearing length, the shearing data is input. After the switch is turned on, the drive motor drives the transmission mechanism to move the knife holder horizontally to cut the material into the required length. The steel coil cut to length line has the advantages of high precision, fast cutting speed, easy operation, simple maintenance, and durability. It is widely used in the processing and sheet metal cutting.
Main components and workflow of metal cut to length machine
1. Feeding device: feeds metal sheets or coils into the production line.
2. Cleaning/pretreatment unit: removes possible dirt or coating.
3. Cutting unit (shear-to-length machine): core equipment, which cuts metal sheets or coils horizontally with a knife.
4. Stacking device: stacks or loads the cut metal sheets onto a transport vehicle.
Working principle of steel coil cut to length line
1. Feeding and pretreatment: Raw materials are fed into the ctl line and go through possible cleaning or pretreatment units.
2. Transverse cutting: Metal sheets or coils are cut by transverse shears to cut them into the required width or length.
3. Stacking and packaging: The cut metal sheets are stacked or loaded, ready for further transportation or processing.
Steel coil cut to length line safety operating procedures
1. Wear work clothes neatly and wear work hats.
2. Before starting, check whether the metal cut to length machine tool handle and operating parts are normal.
3. The material must be clamped correctly and checked whether the leveling and straightening equipment is turned on synchronously.
4. After loading the material, the center positioning should be measured to check whether the hole spacing is correct.
5. The ctl line must be stopped and the speed must be changed. When the machine tool is running, it is strictly forbidden to touch the material with your hands, and the mold and motor cannot be touched with your hands.
6. It is strictly forbidden to place work, measuring tools, gloves and other items on the machine tool guide rails and molds.
7. Do not leave the ctl line tool after starting up, and concentrate on operating.
8. When leaving get off work, wipe the steel coil cut to length line tool, tidy up the site, and cut off the power supply of the machine tool. Lubricate the machine tool gears.
9. During the processing, if the steel coil cut to length line tool is found to have abnormal operation sound or a fault occurs, the power supply should be cut off immediately, the fault should be diagnosed or the manufacturer should be notified.
Metal cut to length machine maintenance
Maintaining the normal operation of metal cut to length machine equipment requires regular maintenance, including but not limited to:
- Clean the ctl line regularly to ensure the smooth flow of cutting tools and transmission parts.
- Check and adjust the metal cut to length machine's tools to ensure the sharpness and fixation of the tools.
- Lubricate the key parts of the metal cut to length machine regularly to extend the service life of the equipment.
Different types of metal cut to length lines
In modern manufacturing, metal cut to length lines are important equipment for metal processing and are widely used in various industries. As an aluminum cut to length line manufacturer with more than 20 years of experience, KINGREAL is committed to designing various types of aluminum cut to length lines according to customers' different production needs and market research to meet different processing needs with rich industry knowledge and technical accumulation.
1. According to the thickness of metal raw materials
1.1 Light gauge metal cut to length line
The light gauge metal cut to length line is designed for processing metal coils with a thickness range of 0.3-3mm. It is suitable for shearing light metal materials such as aluminum alloy, stainless steel, etc., and is widely used in home appliances, automobiles, electronics and other industries. Light gauge metal cut to length lines usually have high-precision shearing capabilities, which can ensure that the sheared edges of each metal sheet are smooth and burr-free, improving the overall quality of the product.
1.2 Medium gauge cut to length machine
The medium gauge cut to length machine can process metal coils with a thickness range of 0.3-6mm, suitable for a variety of medium-thick metal materials. This medium gauge cut to length machine is usually used to manufacture door and window frames, mechanical parts, etc., and the industries involved include construction, machinery manufacturing, and metal products. The flexibility of the medium gauge cut to length machine enables it to adapt to different production needs and maintain high efficiency and high precision.
1.3 Heavy gauge cut to length machine
The heavy gauge cut to length machine is designed for processing metal materials with a thickness range of 6-20mm and is suitable for heavy metal processing. This heavy gauge cut to length machine is mainly used in shipbuilding, heavy machinery, steel structure and other fields, which require strong shearing force and stable performance. The design of the heavy gauge cut to length machine usually adopts high-strength materials to ensure that it can still maintain good shearing effect under high load and ensure the continuity and safety of production.
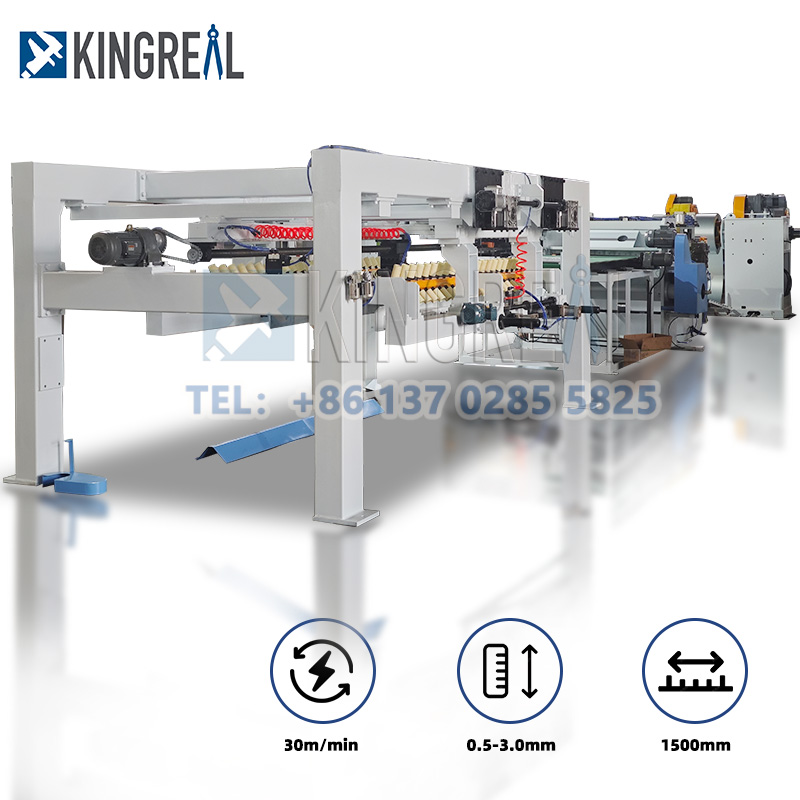
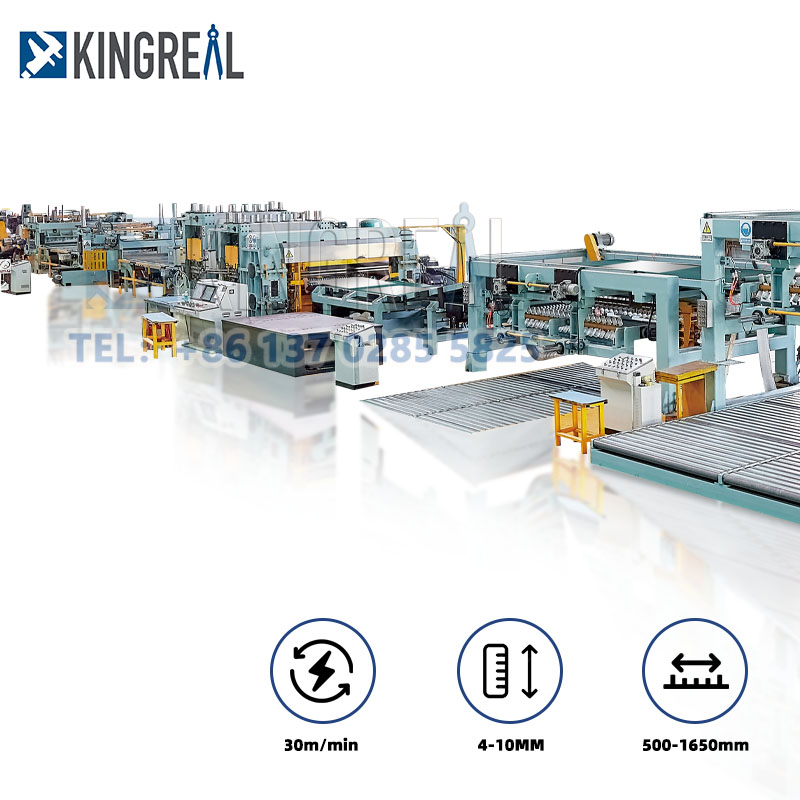
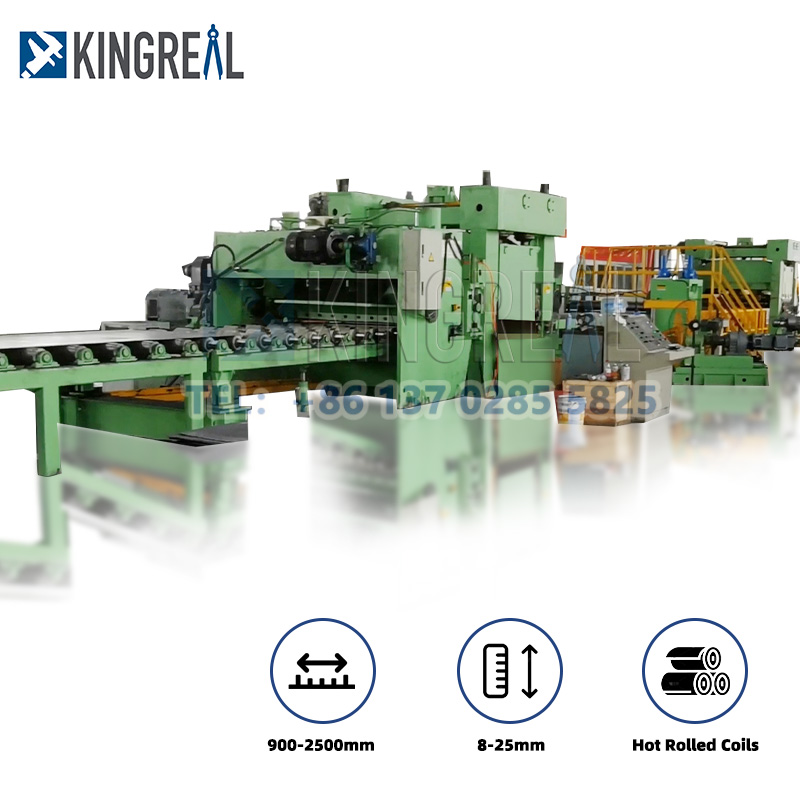
2. According to different shearing methods
2.1 Flying shear metal cut to length line
The flying shear metal cut to length line is known for its high speed and high efficiency. It can process without stopping during the shearing process, which greatly improves production efficiency. Its maximum shearing speed can reach 80m/min, which is very suitable for large-scale production enterprises. This aluminum cut to length line is usually used in high-speed production environments, such as the automotive and electronics industries, and can quickly process large amounts of metal materials.
2.2 Swing shear cut to length line
The swing shear cut to length line also has a high shearing speed, up to 80m/min. It uses a swing shear blade for shearing and is suitable for processing a variety of metal materials. The metal cut to length machine is easy to operate and has low maintenance costs. It is suitable for the production needs of small and medium-sized enterprises and can effectively improve production efficiency.
2.3 Fixed Shear cut to length line
The fixed shear cut to length line needs to be stopped for processing during shearing, and the maximum speed is 50m/min. It is suitable for customers who do not have high requirements for production efficiency.
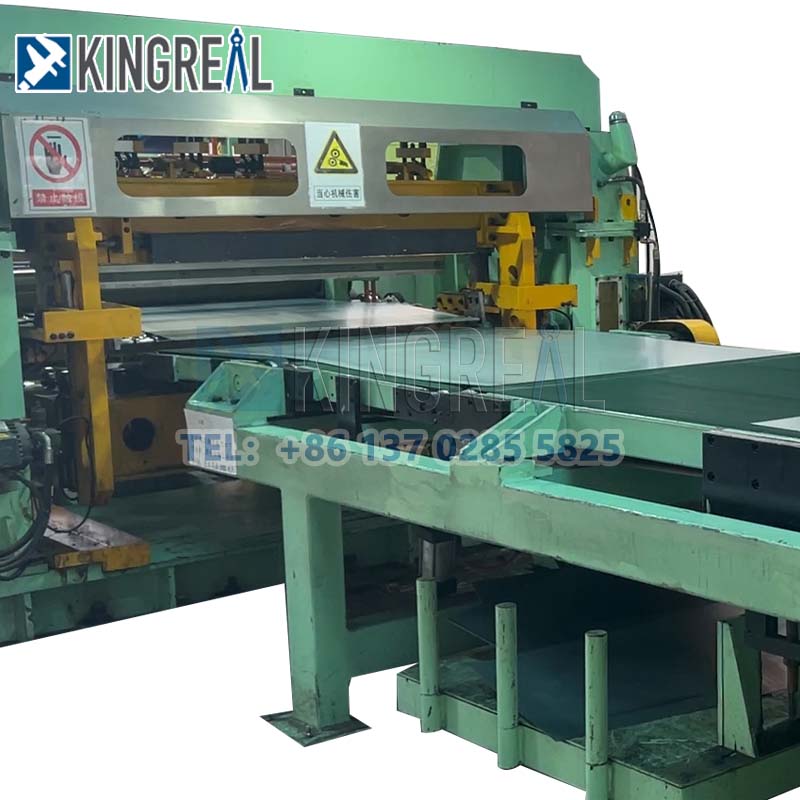
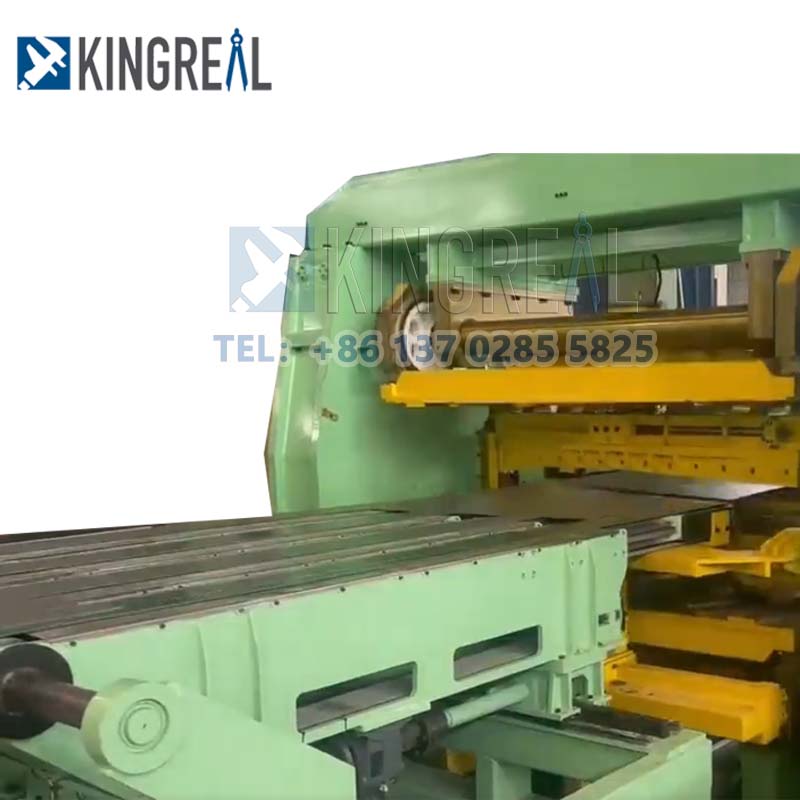
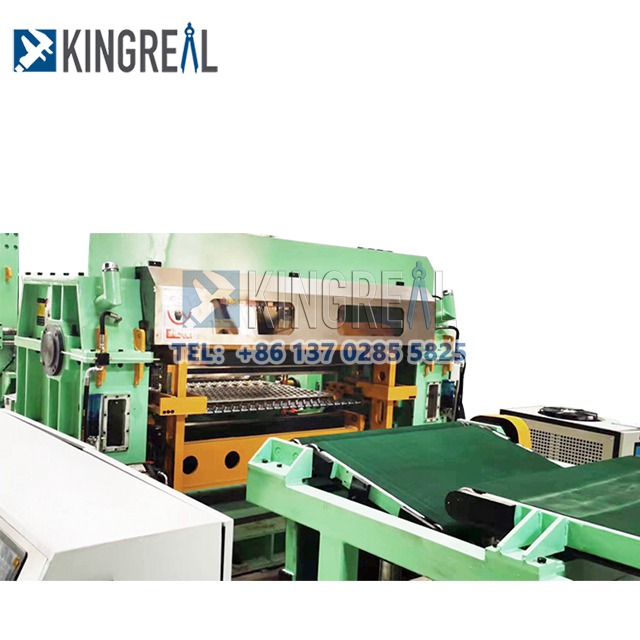
3. Customized needs
In order to meet the special needs of different customers, KINGREAL also provides a variety of customized metal cut to length line solutions.
3.1 Metal cut to length line with double leveler
The aluminum cut to length line is equipped with two leveling machines, and the metal coil needs to go through two leveling processes after unwinding. This design significantly improves the flatness of the metal coil, ensuring higher precision in the subsequent shearing process. The aluminum cut to length line is particularly suitable for industries with extremely high requirements for material flatness, such as electronics and automotive parts manufacturing.
3.2 Aluminum cut to length line with lamination
The aluminum cut to length line is equipped with a special laminating device to prevent the surface of the metal sheet from being scratched during the shearing process. Before entering the aluminum cut to length line, the surface of the metal material will be covered with a protective film to ensure the appearance quality of the final product. This equipment is very suitable for the production of high-end metal products, such as home appliance housings and decorative materials, and can effectively enhance the market competitiveness of products.
3.3 Aluminum cut to length line with double stackers
The aluminum cut to length line is equipped with two stacking tables, which enables metal sheets to be efficiently stacked, significantly improves production efficiency, and reduces dependence on manpower. In a high-volume production environment, the aluminum cut to length line can greatly reduce labor costs and improve overall production efficiency, and is suitable for large manufacturing companies.
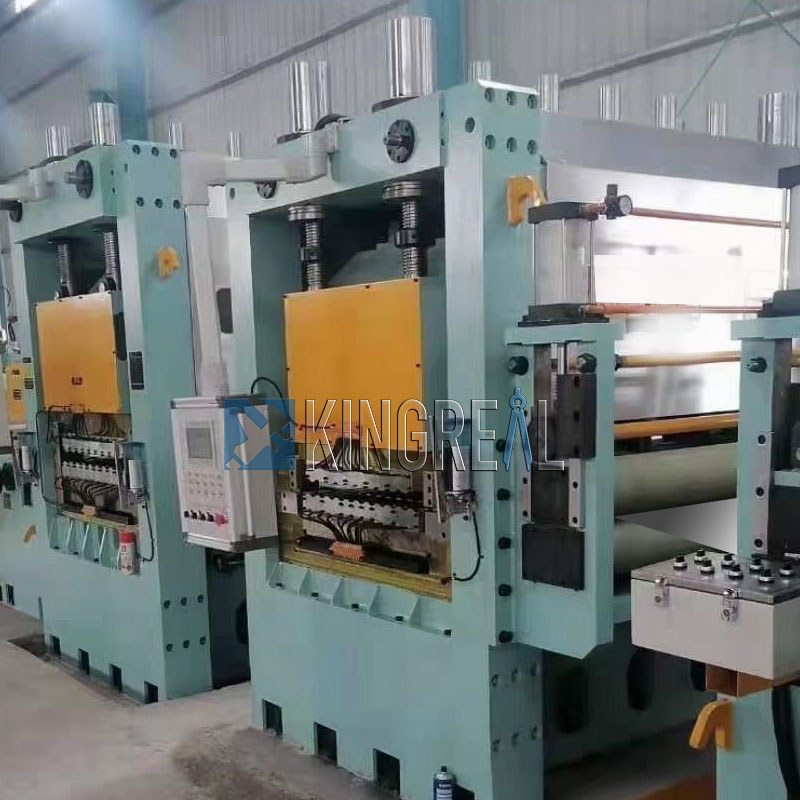
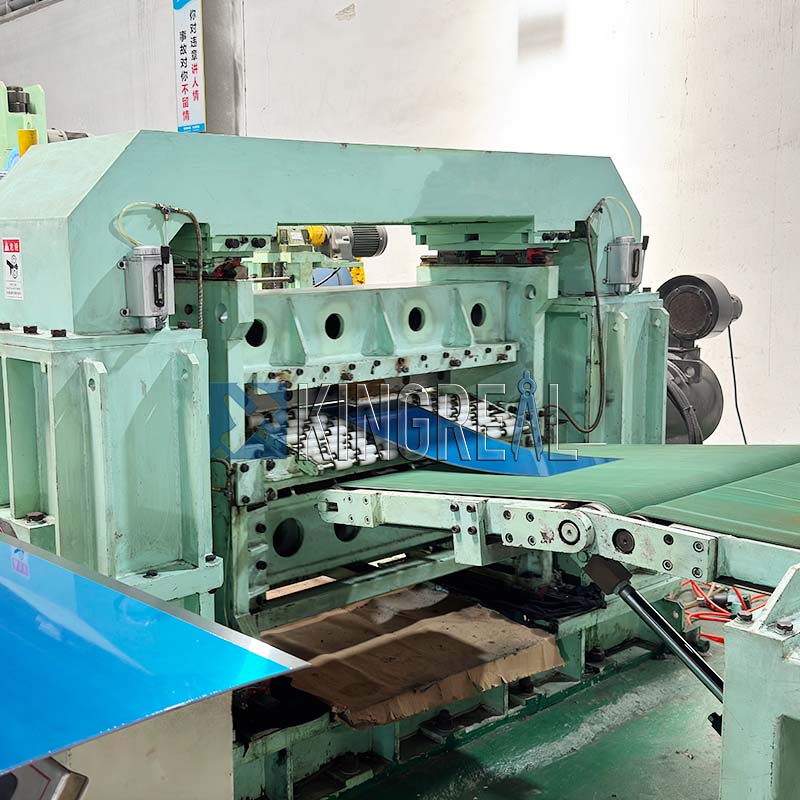
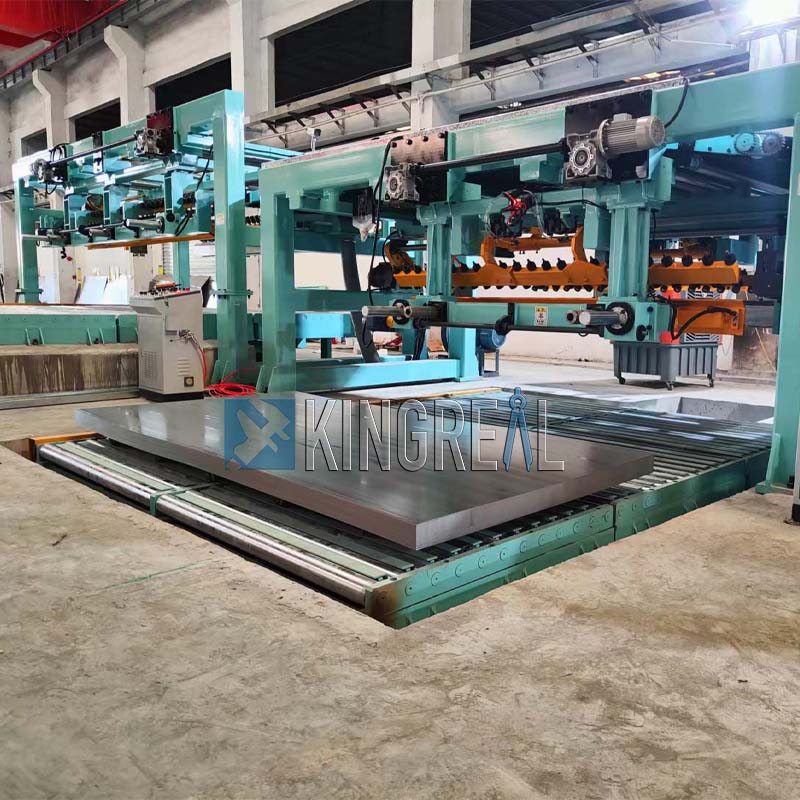