
How to Use Light Steel Frame Machine?
2025-01-09 12:14The automatic production line for light steel villa keels is an efficient and precise equipment used to manufacture keel materials required for light steel structure buildings. The equipment processes the coils into light steel villa keels that meet the design requirements through fully automated operation, and is widely used in villas, commercial buildings and residential projects.
In recent years, light steel villas have become a popular project with their unique advantages, and light steel frame machine has also become a popular cold bending equipment. The light steel villa keel machine produced by KINGREAL cold bending has a fast production speed and can produce a variety of specifications.
The CNC light steel frame machine uses advanced light steel house CAD-assisted design and CAM-assisted production and manufacturing technology. The drawing ability can simultaneously perform 2D and 3D modeling of building structures, interior design and landscape design, realize 3D animation production and accurate engineering construction drawings for keel detail design and production, and accurately calculate reasonable designs according to customer requirements. It can automatically generate material tables and estimation facilities to accurately calculate design costs.
The main production process of the light steel frame machine is: loading - unloading - leveling - feeding - forming - cutting - receiving. The light steel villa keel machine is mainly composed of precision parts such as the unloading machine, guide frame, punching system, forming host, correction device, fixed-length cutting part, material receiving table, intelligent electrical control part, etc.
Many customers do not know how to use the light steel villa keel machine correctly after buying it. Today, this article will share with you how to use the light steel frame machine.
Guide to using the light steel frame machine
1
Preparation work
(1) Check the status of the equipment
- Check whether all parts of the equipment are intact:
- Whether the rotating shaft of the unloading machine is flexible and whether the fixing device is firm.
- Whether there is no foreign matter blocking the leveling device, punching system, roll forming machine and cutting device.
- Ensure that the power supply and air source are connected normally, and the air pressure value meets the equipment requirements (usually between 0.6-0.8MPa).
- Check the lubrication system to ensure that key components (such as molds and roller press bearings) are fully lubricated.
(2) Raw material preparation
- Ensure that the steel coils used meet the specification requirements (width, thickness, material).
- Check the surface of the steel coil for rust, scratches or other defects to avoid affecting production quality.
(3) Safety preparation
- Operators need to wear protective equipment (such as gloves, safety shoes and protective glasses).
- Ensure that the production area is clean and free of debris to avoid interference with material or equipment operation.
2
Equipment startup
(1) Loading steel coils
- Use lifting equipment to place the steel coil on the unloader.
- Adjust the tensioning device of the unloader to ensure that the steel coil is firmly fixed and can rotate smoothly.
(2) Threading process
- Pass the front end of the steel strip through the following components in sequence:
- Leveling device: Ensure that the steel strip is flat and wrinkle-free.
- Punching system: Align the center line of the punching die to ensure the correct path of the steel strip.
- Roller forming machine: Place the steel strip in the guide rail to ensure that the position is centered.
- Cutting device: Ensure that the steel strip can pass through the cutting knife area smoothly.
(3) Set parameters
- Turn on the control system and set production parameters through the touch screen or computer interface:
- Specification parameters: Enter the width, height and thickness of the keel.
- Punching design: Select the hole position and hole type according to the drawing, and set the hole spacing.
- Cutting length: Enter the length requirement of each keel.
- Check and save the settings to ensure that the parameters are correct.
(4) Start the equipment
- Press the start button, the equipment starts running and enters the automated production state.
- When starting for the first time, it is recommended to run in low speed mode to observe whether each component is working properly.
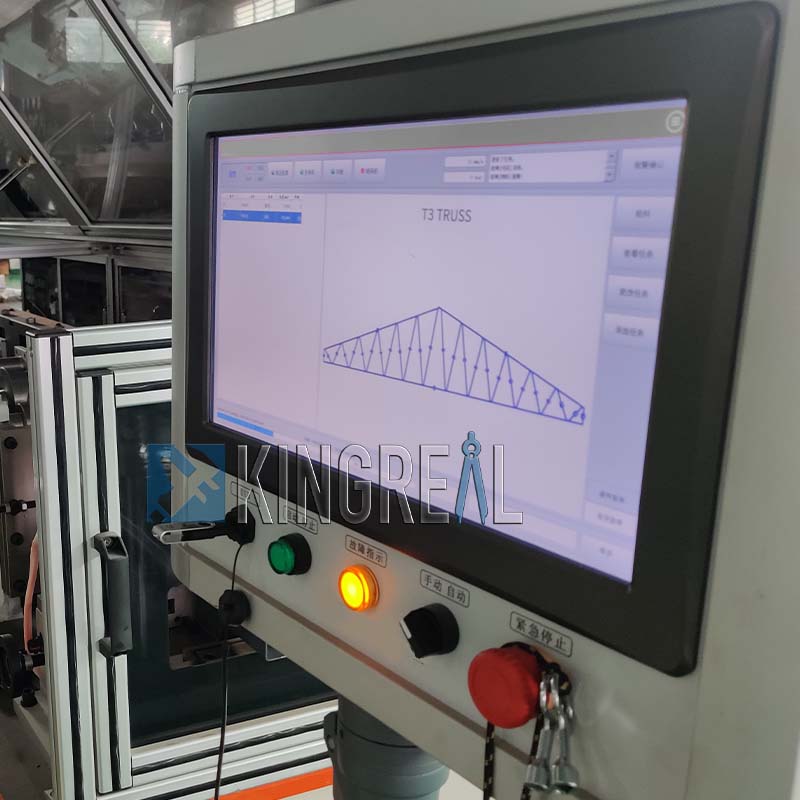
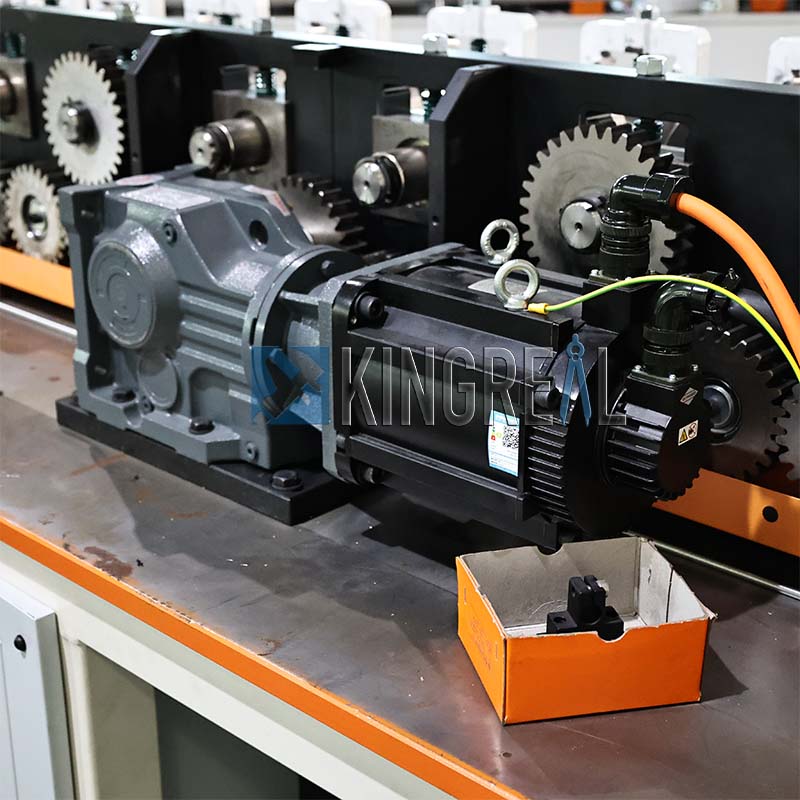
3
Production process
(1) Leveling and feeding
- The unloader feeds the steel strip into the leveling device, and the leveling device straightens the steel strip to ensure that it is flat and wrinkle-free.
- The automatic feeding device evenly feeds the leveled steel strip into the punching system.
(2) Punching operation
- The punching system automatically punches holes according to the set program.
- The punching die is driven by hydraulic or servo to complete the high-precision punching operation.
- Real-time monitoring of the punching position and hole type to ensure consistency with the design drawings.
(3) Roll forming
- The steel strip enters the roll forming machine and is gradually formed by multiple sets of rollers to form the specified keel section.
- During the rolling process, check whether the material is offset or deformed, and adjust the guide rail or roller spacing if necessary.
(4) Cutting the finished product
- The formed keel is cut into a set length by the cutting device.
- The cutting method is usually hydraulic cutting or servo cutting to ensure that the cut is smooth and burr-free.
- After cutting, the finished product automatically slides to the finished product collection table.
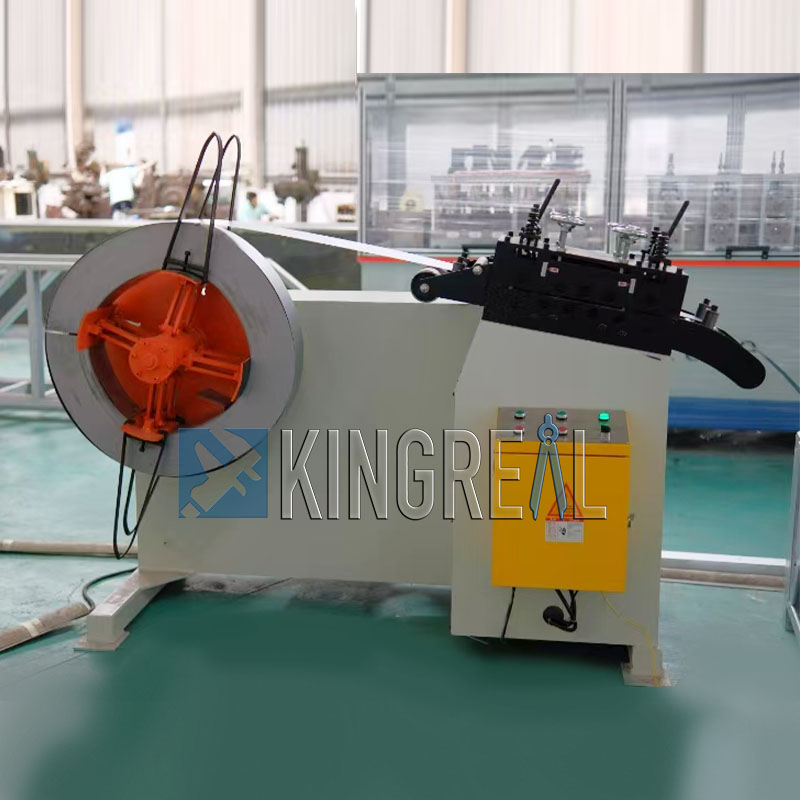
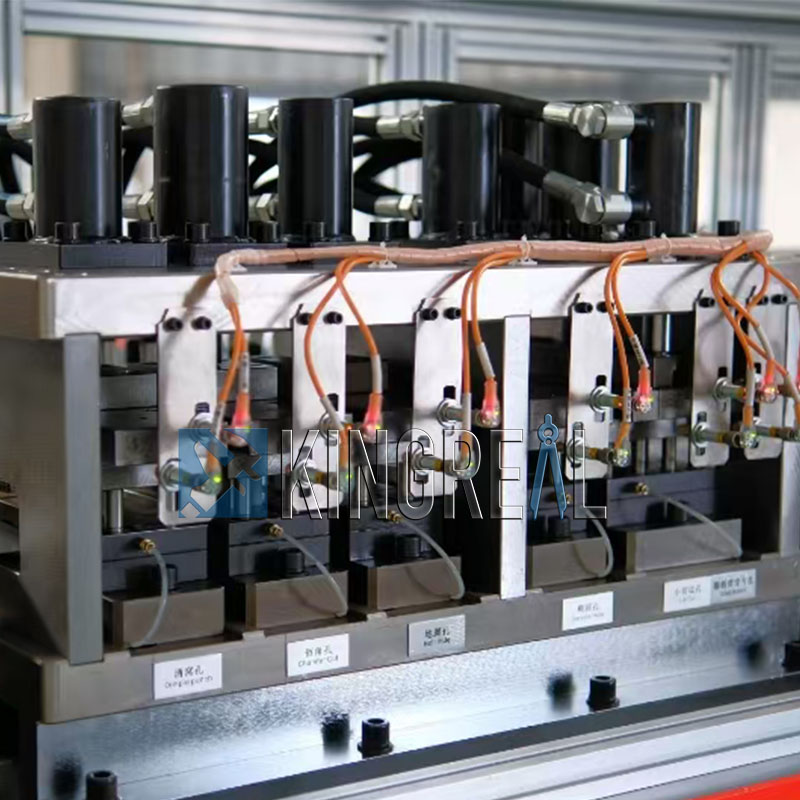
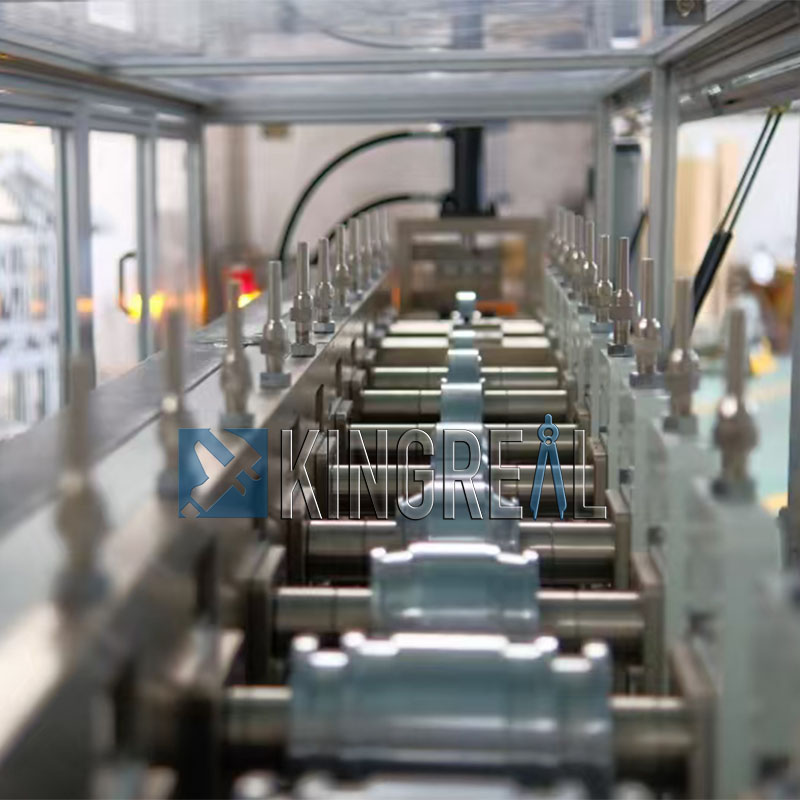
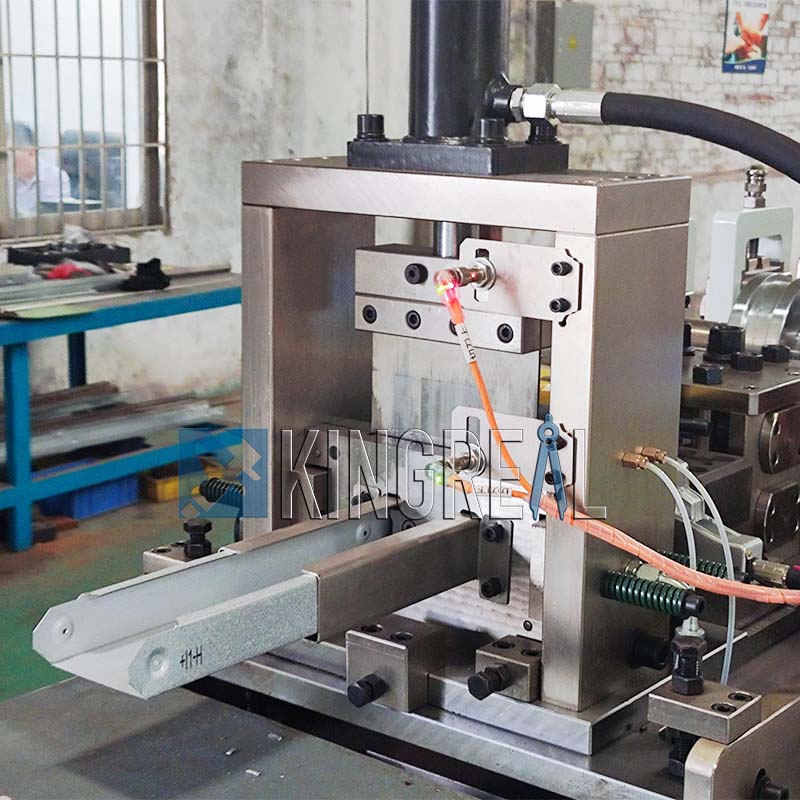
4
Production monitoring
(1) Real-time monitoring of equipment operation status
- Observe the feeding speed, punching accuracy, forming effect and cutting length through the control panel.
- If an abnormality is found (such as punching offset, material jamming, etc.), press the emergency stop button immediately, and continue to run after troubleshooting.
(2) Regularly check production quality
- Randomly select finished products to check dimensional accuracy, hole position and surface quality.
- If there is a deviation, adjust the corresponding parameters or mold position.
5
End operation
(1) Stop the light steel frame machine
- After completing production, press the stop button and wait for the light steel villa keel machine to stop running completely.
- Turn off the power and air supply to ensure that the equipment is in a safe state.
(2) Cleaning and maintenance
- Clean the surface of the light steel villa keel machine and the working area to remove iron filings and dust.
- Check the wear of the mold, roller and cutter, and replace or repair them if necessary.
- Lubricate the moving parts to ensure smooth operation of the equipment next time.
(3) Finished product processing
- Stack qualified finished products according to specifications and mark them with clear labels.
- Mark or handle defective products to avoid mixing with qualified products.
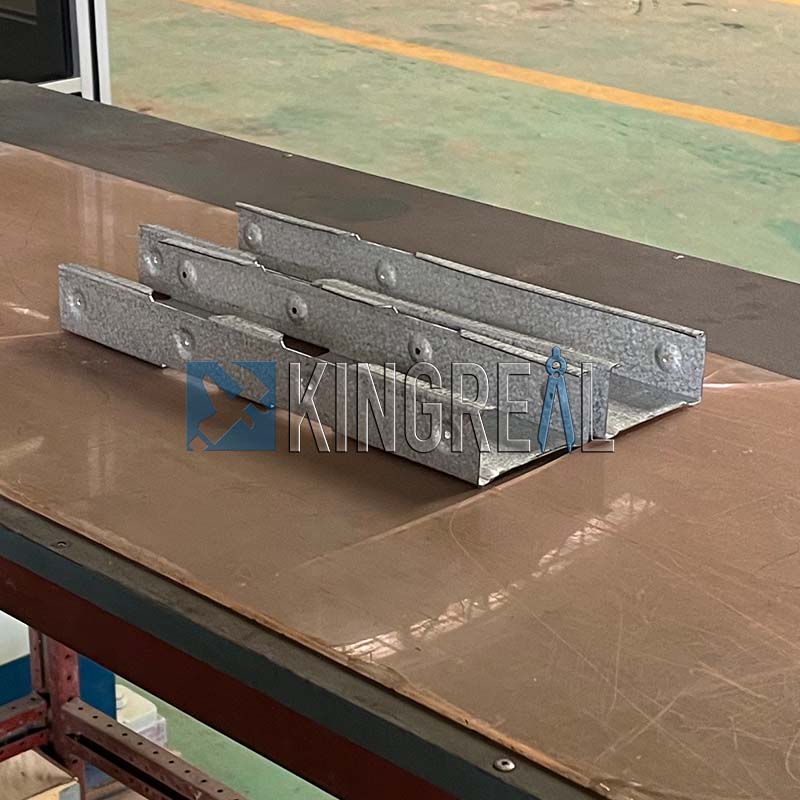
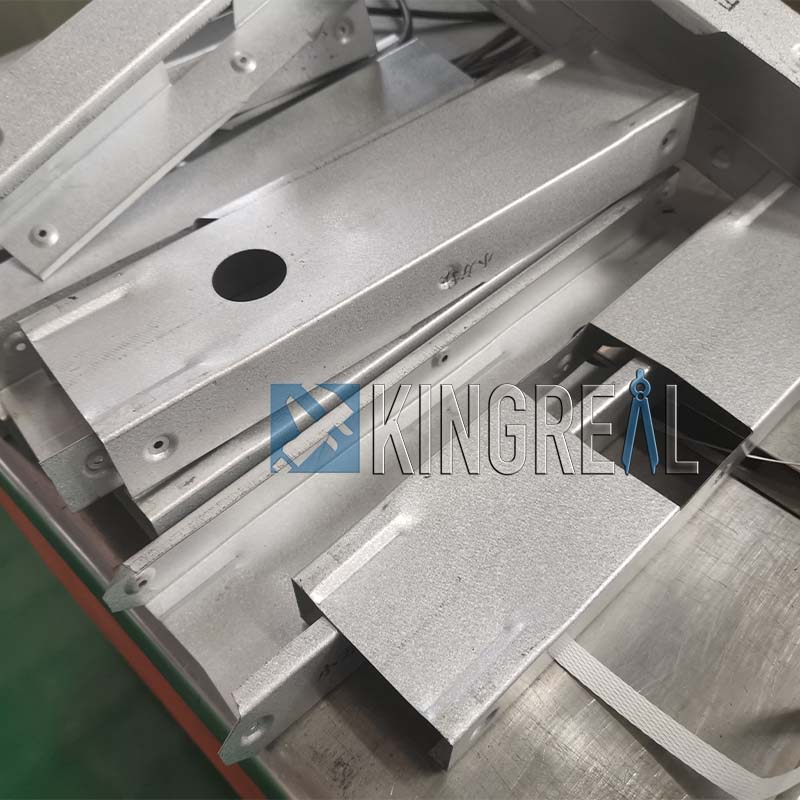
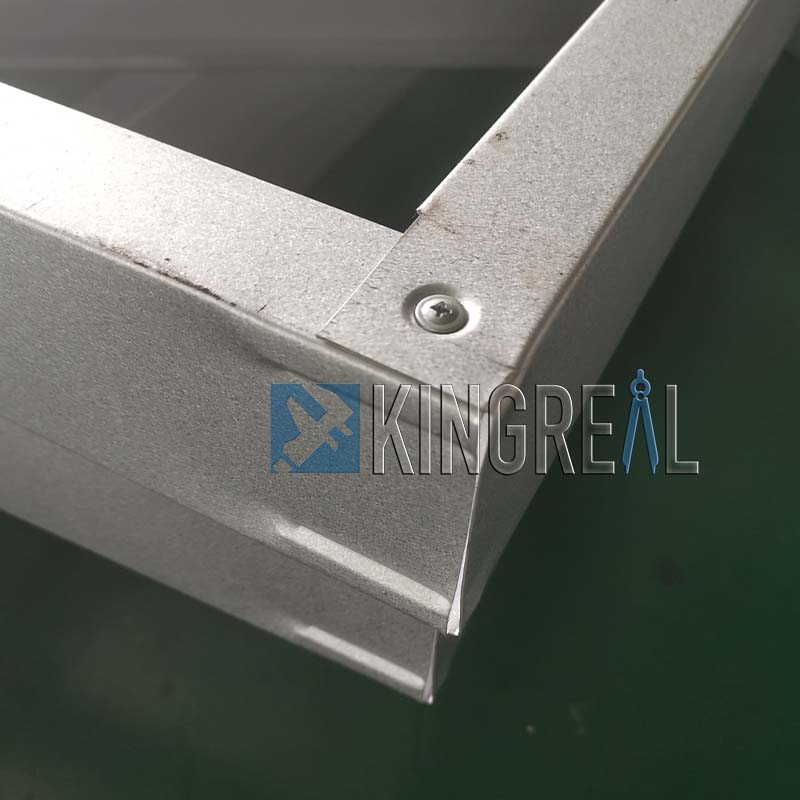
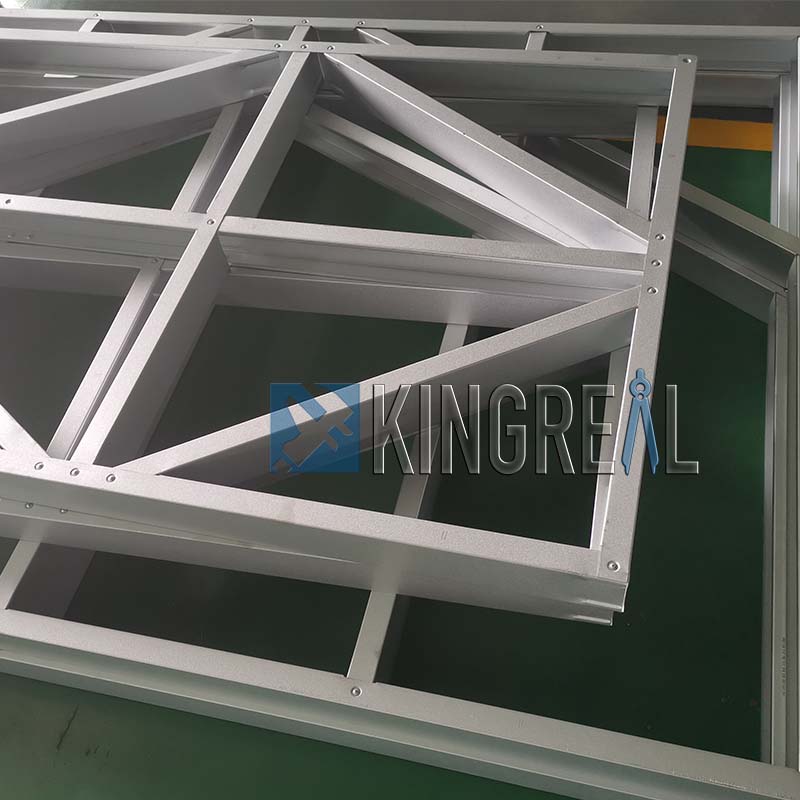