
How to use the cable tray machine?
2025-03-04 12:00Definition of cable tray production line
The cable tray machine is a device specially used to manufacture cable trays. Cable trays are an indispensable part of the power and communication industries. They are widely used to support and protect cables and ensure the safety and stability of cables. With the continuous development of the power and communication industries, the demand for cable trays is also growing. Therefore, the importance of cable tray making machines in the market and industry is becoming increasingly prominent.
The cable tray production line can efficiently produce cable trays of various specifications and types through a series of processing processes, including unwinding, leveling, punching, forming, cutting and discharging. These formed bridges not only have good mechanical strength and corrosion resistance, but also can meet the use requirements in different environments.
Main components of the cable tray making machine
The cable tray production line consists of multiple key components, each of which plays an important role in the entire production process. The following is a brief introduction to the main components:
Decoiler
The decoiler is the first process of the cable tray making machine, which is mainly used to unwind the coil and send it to the subsequent processing link. The working principle of the decoiler is to drive the reel through the motor and control the tension of the coil to ensure the uniform feeding of the material. The stability and accuracy of the decoiler directly affect the subsequent leveling and forming effects.
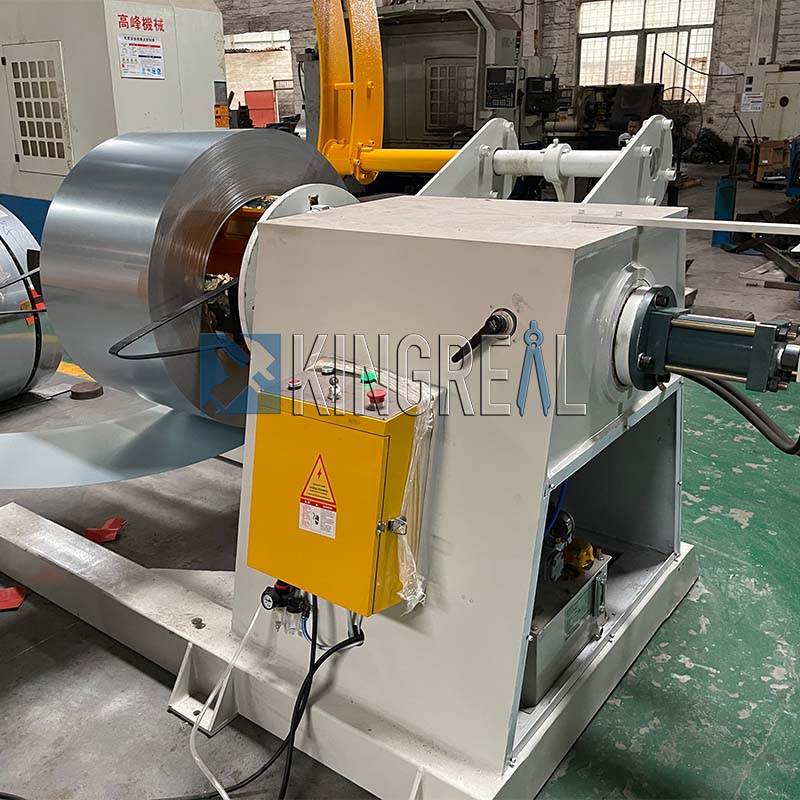
Straightener
The precision straightener is used to level the coil to make its surface flat and smooth for subsequent punching and forming. The straightener is usually equipped with multiple sets of leveling rollers. By adjusting the pressure and spacing of the rollers, the corrugation and bending of the material are eliminated. The leveled material can effectively improve the quality of subsequent processing and ensure that the formed bridge has good appearance and strength.
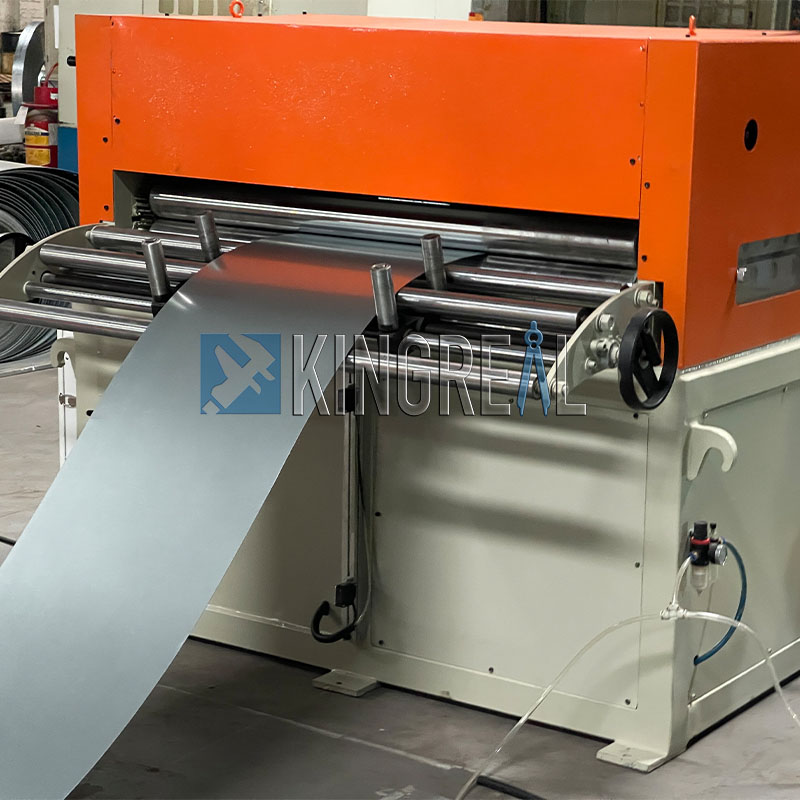
Punching station
The punching station is responsible for punching holes on the leveled material to form the required holes for subsequent installation and wiring. The punching station controls the position, size and spacing of the holes through the mold to ensure the accuracy of each hole. The efficient punching process not only improves production efficiency, but also reduces labor costs.
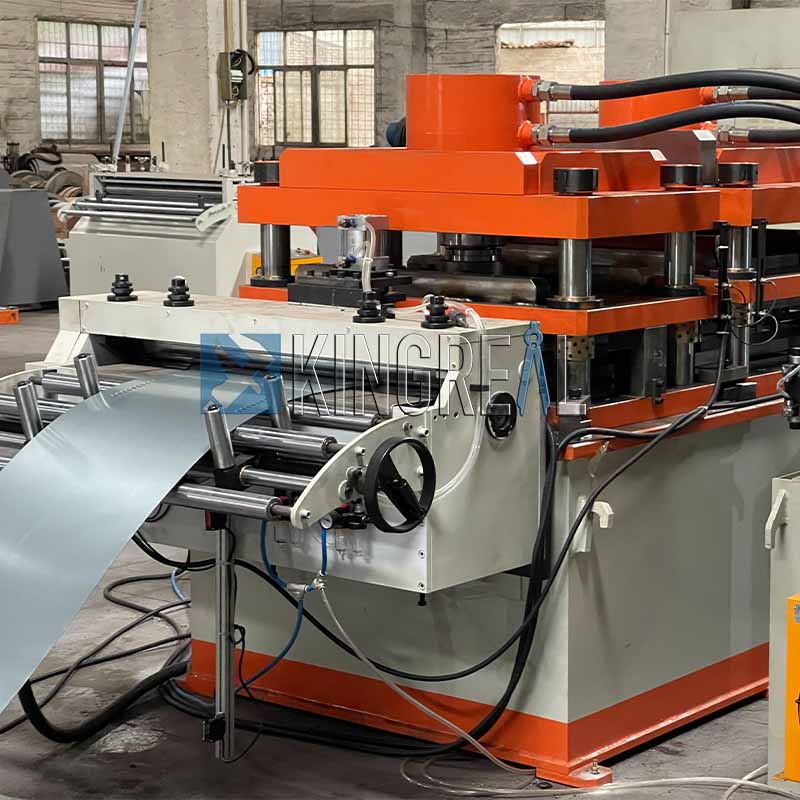
Roll forming machine
The roll forming machine is the core component of the cable tray production line, which is responsible for processing the material into the final cable tray shape through a series of forming rollers. The roll forming machine usually adopts a continuous forming method. By adjusting the configuration and pressure of the rollers, cable trays of different specifications and shapes can be produced.
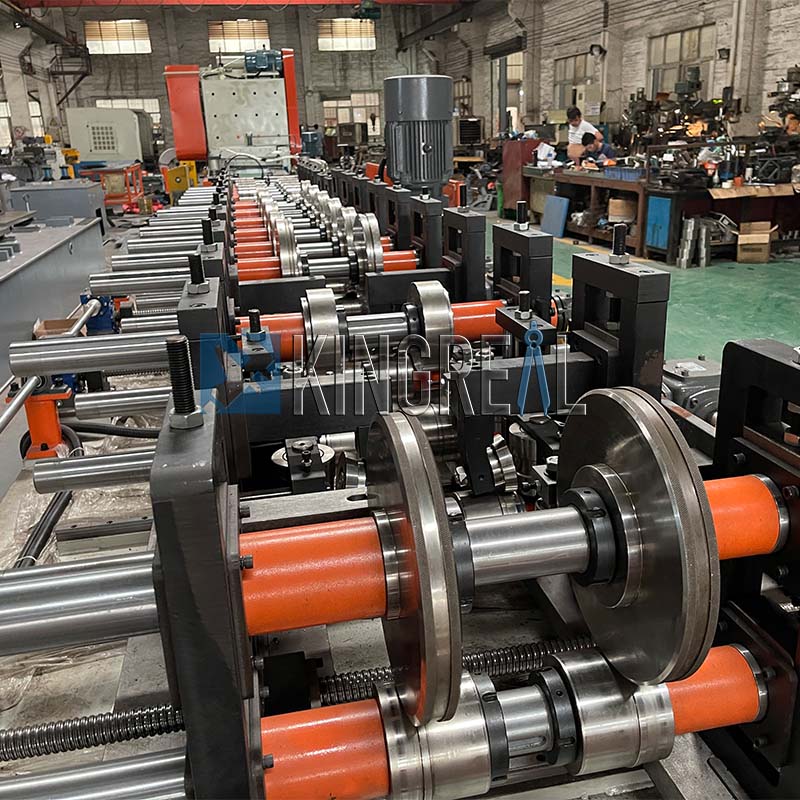
Cutting station
KINGREAL equips the cable tray making machine with precision cutting station. It is used to cut the formed cable tray into the required length. The accuracy and efficiency of the cutting station directly affect the quality and delivery cycle of the finished product. Modern cutting stations are usually equipped with automatic measurement and control systems, which can realize automatic operation and improve production efficiency.
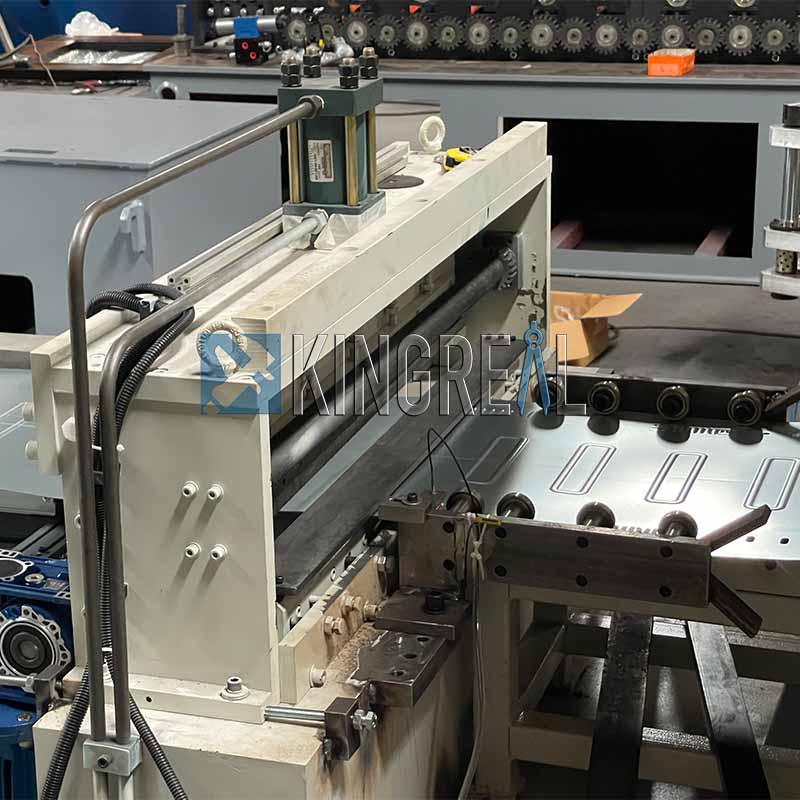
Instructions for using cable tray making machine
Video about cable tray making machine:
The process of using the cable tray production line can be divided into several steps, and each step is crucial. The following is a detailed operation guide combined with the workflow:
Before using the cable tray making machine, adequate preparation is an important part of ensuring smooth production and finished product quality. The following are detailed preparation steps, covering equipment inspection, material preparation, safety protection and other aspects.
1. Cable tray production line inspection
Cable tray production line inspection is the first step in preparation to ensure that all parts of the cable tray production line are operating normally to avoid downtime or product quality problems due to cable tray production line failure. The content of cable tray making machine inspection includes:
1.1 Appearance inspection
- Overall appearance: Check the overall appearance of the cable tray production line to ensure that there is no obvious appearance damage or rust.
- Component integrity: Check whether all parts are complete, especially the various parts of the decoiler, straightener, punching machine, roll forming machine and cutting station.
1.2 Functional inspection
- Decoiler: Check whether the motor is running normally and whether the tension of the reel is appropriate. Ensure smooth feeding without slipping or jamming.
- Straightener: Check the wear of the leveling roller to ensure that the spacing and pressure of the roller can be adjusted in place to ensure the flatness of the material.
- Punching station and punching press: Check whether the mold is firmly installed and confirm whether the punching position, size and spacing are set correctly. Ensure that the pressure of the press meets the material requirements.
- Roll Forming machine: Check whether the configuration of the forming roller is correct to ensure that the required specifications of the bridge can be produced.
- Cutting station: Check the sharpness of the knife to ensure cutting accuracy.
1.3 Electrical system inspection
- Power connection: Ensure that the power connection is safe, the wiring is not loose, and the cable is not damaged.
- Control panel: Check whether the switches, buttons and display screens on the control panel are working properly to ensure that the equipment operation can be accurately controlled.
2. Material preparation
Material preparation is a key link that affects the quality of the finished product. Choosing the right raw materials can improve production efficiency and product quality. The content of material preparation includes:
2.1 Material selection
- Material type: Cable trays are usually made of cold-rolled steel, galvanized steel or aluminum alloy. When selecting, the corrosiveness and strength requirements of the use environment should be considered.
- Material specifications: Select the appropriate material width and thickness according to production needs to ensure that it meets the design requirements.
2.2 Material Inspection
- Quality Inspection: Check the quality of raw materials, including surface finish, thickness uniformity, etc., to ensure there are no defects.
- Quantity Confirmation: Confirm the quantity of materials according to the production plan to ensure sufficient supply to avoid production stoppages.
2.3 Material Storage
- Storage Environment: Ensure that the materials are stored in a dry and ventilated environment to avoid moisture causing rust on the materials.
- Label Management: Clearly label materials of different specifications for easy subsequent use.
3. Safety Protection
Safety protection is an important part of the production process that cannot be ignored. Operators must strictly abide by safety operating procedures to ensure the safety of themselves and other staff. Safety protection includes:
3.1 Personal Protective Equipment
- Safety Shoes: Wear safety shoes that meet the standards to prevent injuries caused by heavy objects falling.
- Protective Gloves: Use wear-resistant and cut-resistant protective gloves to avoid hand injuries.
- Goggles: Wear goggles to prevent metal chips or other foreign objects from flying into the eyes.
- Earplugs: Wear earplugs to protect hearing in noisy environments.
3.2 Safety signs and warnings
- Warning signs: Set up obvious safety signs around the cable tray production line to remind operators to pay attention to safety.
- Emergency stop button: Make sure the emergency stop button is clearly located and can be used at any time to quickly stop the cable tray making machine in an emergency.
3.3 Operator training
- Training content: Provide comprehensive training for operators, including cable tray making machine operation, troubleshooting and safety precautions.
- Practical exercises: Through practical exercises, ensure that operators can master the use of cable tray making machine and emergency handling capabilities.
4. Environmental preparation
Ensuring the cleanliness and safety of the production environment will help improve work efficiency and reduce accidents.
4.1 Workshop cleaning
- Clean the workbench: Ensure that the workbench is free of debris and tool residues and keep it clean.
- Floor cleaning: Clean the floor to avoid slips or trips caused by debris on the floor.
4.2 Ventilation and lighting
- Ventilation facilities: Ensure that the workshop is well ventilated to avoid smoke or odor affecting the health of operators.
- Lighting conditions: Ensure that the workshop is well lit to avoid operating errors due to insufficient light.