
What is a perforated sheet used for?
2024-11-18 20:17What is a Perforated Sheet?
A perforated sheet is a material, typically made from metal, that has been punched with a pattern of holes or slots. And these metal perforated plates are made by metal sheet perforation lines. These holes can vary in size, shape, and spacing depending on the intended use. The primary purpose of perforation is to enhance the material's functionality and aesthetics, making it widely applicable in various fields.
Modern perforated sheets can be made from various materials, with the most common being metals such as stainless steel, aluminum, and brass. Each of these materials offers distinct advantages that cater to different application needs. For example, perforated sheet metal made of stainless steel is corrosion-resistant, making it suitable for harsh environments; aluminum perforated plates are lightweight and easy to install, ideal for applications requiring frequent relocation; and plastic perforated sheets possess excellent chemical resistance, suitable for certain specialized industrial environments.
The design of a perforated plate is also highly versatile, allowing for the creation of various hole shapes and patterns based on specific requirements. Common perforation patterns include round holes, square holes, rectangular slots, and hexagonal holes. Each pattern serves unique purposes: round hole perforated sheets are often used for general filtration and ventilation; square hole perforated sheet metal is favored for applications needing high breath-ability due to its larger open area; and rectangular and hexagonal hole perforated plates are preferred in certain industrial applications due to their unique structural properties.
This wide range of designs and materials makes perforated sheets incredibly useful and adaptable to many different uses, providing both functionality and visual appeal.
How are Perforated Sheets Produced?
Perforated sheets are typically manufactured using advanced machinery, such as the KINGREAL Metal Perforated Making Machine. The production process involves several key steps to ensure precision and quality:
Decoiler: The process begins with decoiler, where large coils of metal are unwound to create flat sheets. This prepares the material for further processing.
Leveling: The sheets are then leveled to ensure uniform thickness and flatness. This is crucial for achieving consistent perforation quality.
Feeding: The leveled sheets are fed into the perforating machine. The feeding mechanism ensures that the sheets move smoothly and at a constant speed into the perforation unit.
High-Speed Perforation: Using high-speed perforation tools, the machine punches holes into the metal sheets. This can be done using various techniques such as rotary pinned perforation rollers or high-precision punch presses. The pattern, size, and shape of the holes are determined by the design requirements.
Feeding and Precision Cutting: After perforation, the sheets are fed further and cut to precise lengths. This ensures that each perforated sheet metal piece meets specific dimensional requirements.
In addition to producing perforated sheets, the KINGREAL Metal Perforated Making Machine also supports the production of perforated coils and secondary processing of perforated raw materials. This versatility makes it a valuable asset in various manufacturing setups.
Each perforated plate produced by the KINGREAL Metal Perforation Line undergoes strict inspection to ensure uniformity and adherence to specific standards and specifications. Quality control is a critical component of the entire production process. Through rigorous quality inspections, it is ensured that each perforated plate leaving the factory meets customer requirements. In modern manufacturing, automated quality inspection equipment, such as visual inspection systems and measuring instruments, are typically used to enhance detection efficiency and accuracy.
The meticulous process ensures that the final perforated sheets are not only functionally efficient but also meet the highest standards of quality and precision, catering to a wide range of industrial and commercial applications.
Video About Coil Perforation Line
Classification of Perforated Sheets by Hole Pattern
Round Holes: The most common pattern used for general purposes. Perforated sheets with round holes are valued for their simple structure, high strength, and high open area. They are widely used in screening, filtering, and ventilation. The size and spacing of the round holes can be adjusted according to specific requirements to meet various application needs.
Square Holes: Provide a larger open area, making them ideal for architectural designs. Perforated sheet metal with square holes is favored for its aesthetic appearance and high open area, often used in architectural decorations, ceilings, and curtain walls. The shape and arrangement of the square holes can be customized according to the designer's needs, offering a high degree of flexibility.
Hexagonal Holes: Offer a high open area and unique visual effects, commonly used in high-strength applications. Perforated plates with hexagonal holes feature a distinctive honeycomb structure, providing high strength and rigidity. These are widely used in aerospace, automotive, and architectural sectors. The shape and arrangement of hexagonal holes can be tailored to specific requirements to achieve optimal structural performance.
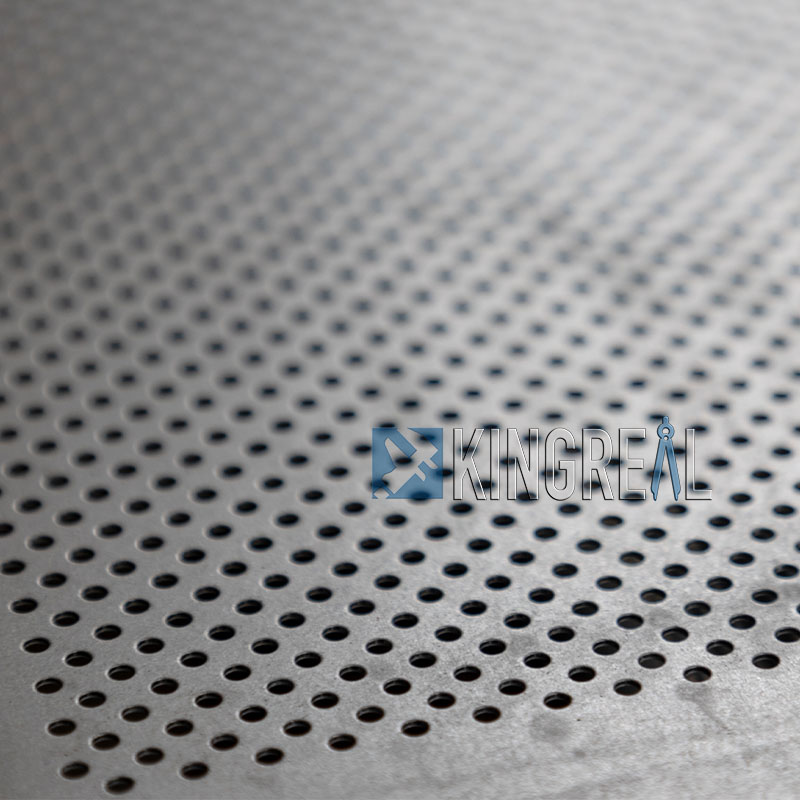
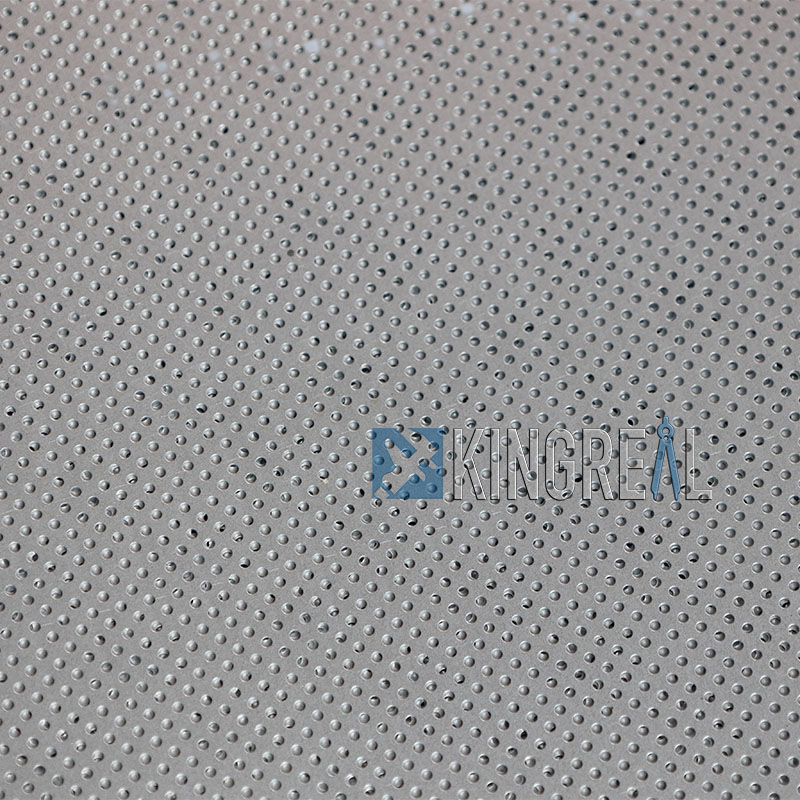
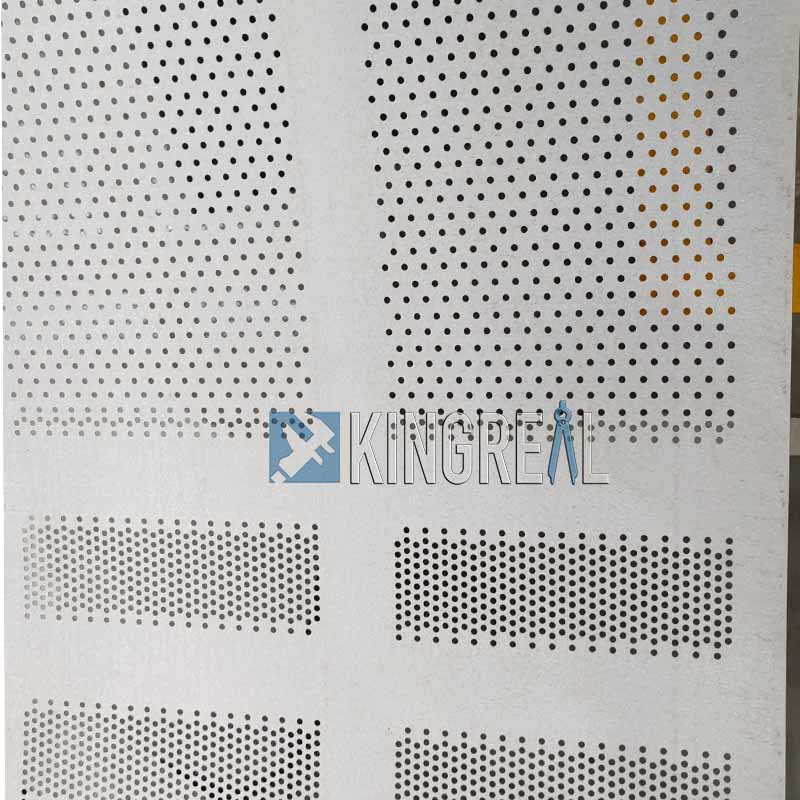
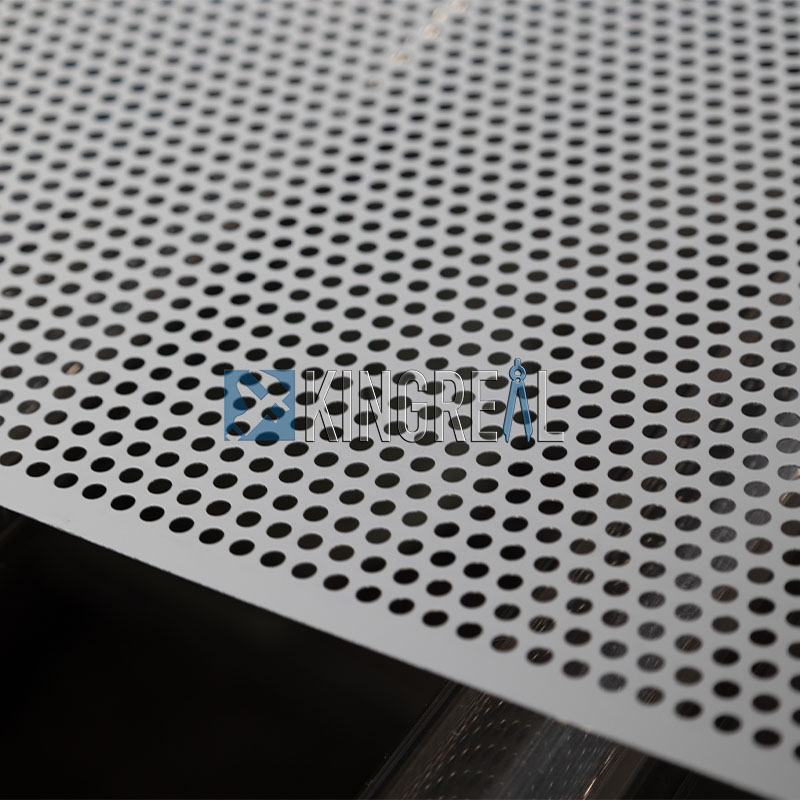
These diverse perforation patterns make perforated sheets highly versatile and suitable for a wide range of applications, combining functionality with aesthetic appeal to meet the demands of various industries.
Classification of Perforated Sheets by Material
Stainless Steel: Known for its corrosion resistance and strength, stainless steel perforated sheets are commonly used in environments requiring durability. These perforated plates boast excellent mechanical properties and longevity, making them suitable for harsh conditions such as chemical plants and marine engineering. Additionally, stainless steel offers good weldability and machinability, allowing for various processing and welding methods to meet different requirements.
Aluminum: Lightweight and resistant to corrosion, aluminum perforated sheet metal is ideal for applications that require easy installation and long service life. Aluminum's properties make it popular in the aerospace, transportation, and architectural decoration sectors. Its density is only one-third that of stainless steel, making it a favored choice for applications demanding weight reduction.
Brass: Due to its aesthetic appeal, brass perforated plates are often used for decorative purposes while also providing good corrosion resistance. Brass perforated sheets have a unique golden luster and excellent machinability, commonly utilized in high-end decor, artisanal crafts, and musical instrument manufacturing. Brass also possesses good electrical conductivity and antibacterial properties, making it valuable for certain electronic components and medical devices.
This classification by material highlights the diverse applications and benefits of perforated sheets, allowing for optimal selection based on specific environmental and functional requirements.
"Common Industry Applications of Perforated Sheets"
Construction Sector In architectural design, perforated sheets are commonly used for the decoration of exterior walls and facades. Thanks to their unique hole patterns, these sheets can create rich visual effects, giving buildings a distinctive appearance. Additionally, perforated sheets can regulate light and air flow, providing natural ventilation and shading, which helps improve the energy efficiency and comfort of buildings.
Perforated sheets are also widely used in interior decoration, such as ceilings, partitions, and decorative walls. Their various hole patterns and material choices enable them to meet diverse design needs, offering both practicality and aesthetic appeal. For example, in commercial spaces, perforated plates can create a modern and stylish office environment; in home decor, they can be used to enhance wall designs, adding depth and sophistication to the overall interior design.
Automotive Industry In the automotive sector, perforated sheet metal is often used to manufacture heat dissipation and ventilation components such as radiators, coolers, and ventilation grilles. The high open area and durability of these sheets allow for effective heat dissipation and ventilation, ensuring the proper functioning of automotive parts. Moreover, the lightweight nature of perforated sheets helps reduce the overall weight of the vehicle, thereby improving fuel efficiency. Perforated sheets are also used to make automotive soundproofing and damping materials. Their porous structure can effectively absorb and attenuate noise, enhancing the quietness and comfort of the cabin. Additionally, the high strength and durability of perforated plates can enhance the overall safety performance of vehicles.
Filtration and Separation Equipment Perforated sheets are crucial in manufacturing industrial filtration and separation equipment such as centrifuges, separators, and filters. Their precise hole designs allow for effective filtration and separation of materials of different particle sizes, ensuring smooth production processes. The materials chosen for these perforated plates are typically corrosion-resistant stainless steel, ensuring long-term use of the equipment in harsh environments.
The above are the typical applications of perforated sheets. KINGREAL MACHINERY, as a professional manufacturer of Metal Perforated Making Machines, possesses a high level of expertise in the field of machine manufacturing. If you have any other questions, feel free to contact us!